Putaway processes in logistics
In the Putaway business process, items are received, transported and stored in the warehouse. The items can be identified and assigned to a storage location using labels that were previously attached in the goods receipt business process. After a successful incoming goods inspection, the inventory is passed on from goods receipt to putaway, a process consisting of individual process steps. Accordingly, typical tasks that take place during putaway are, for example
- Acceptance of the transport order
- Identification of the item
- Receiving the item
- Transporting the item to the warehouse
- Placing the item in the corresponding storage compartment
Some types of warehouse, such as the high-bay warehouse or the automated small parts warehouse (AS/RS), have a pre-zone (see below). From there, the inventory is picked up and stored. During putaway, the inventory is initially receipted as a lump sum, individually or online. The method of confirmation depends on which resources are available. For example, whether a warehouse management system, a radio terminal or an automatic storage and retrieval machine is used in the warehouse. Like the acknowledgement, the type of compartment allocation is also different. It can be triggered by the system, by the user or by a system proposal for the storage compartment that can be changed by the user.
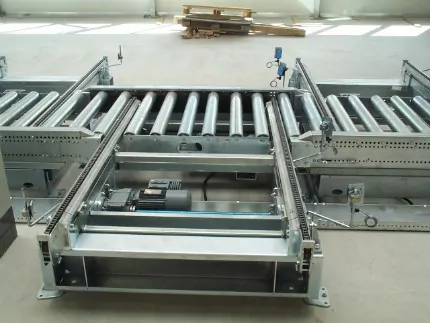
Allocation of the storage compartment during putaway
The allocation of the storage compartment is generally influenced by various aspects, such as
- Physical requirements on the part of the stored goods
- Safety and legal requirements
- Operational optimization
The ideal solution is to move the stored goods quickly to an approved storage location, because it is not just about being effective, but above all about being efficient. The storage compartment volume should be used optimally (physical requirement). It is also important to observe prohibitions on storing certain items together and to comply with the maximum permissible shelf load (safety and legal requirements). Finally, operational processes can be improved by minimizing travel and transport routes or by making maximum use of existing storage capacities (operational optimization). The optimal implementation of or compliance with these criteria helps to ensure that the subsequent processes after storage in a compartment are subject to no or only minimal restrictions.
Storage – the key figures
The efficiency, productivity and quality of putaway can be assessed on the basis of corresponding warehouse key figures.
From this process, the number of putaways and items as well as the number and distance of storage locations are important for the control center.
The key figures for the following processes play a role in measuring the putaway targets: number of putaways, capacity utilization, putaway time, work progress, quality of putaway.
The recipients of the key figures are the logistics manager, the warehouse manager and other employees who play a role in transportation.
Putaway – the pre-zone
After delivery to goods receipt, the inventory is either picked up manually or automatically transported to the warehouse using materials handling technology. Some types of warehouse often also have a pre-zone from where the inventory is picked up and stored. If the warehouses are operated automatically, storage and material removal are carried out using automatic storage and retrieval machines.
Information about the inventory to be stored, such as the type of goods, item number, quantity and weight, is recorded. Digital recording via RFID or barcodes is often used to identify the inventory. The data is usually recorded using sensors or scanners.
Scanning a barcode on the items ensures exact identification; this is so important because only clearly identified inventory enables efficient management in the first place. The warehouse management system uses the scanned information to determine the optimum storage location and updates the stock file.
Further information on system-side storage bin allocation:
- ABC analysis in inventory management
- Overview of allocation strategies
- Storage zones and the cube-per-order index
The counterpart to the pre-zone is the retrieval area, where the inventory is placed after retrieval. From there, the inventory is transported to picking or goods issue.
Putaway – Receipt and compartment allocation
Various forms of confirmation are available for putaway:
A – The blanket acknowledgement of putaway for an entire load
This only makes sense if the warehouse management system has previously assigned compartments and is a rather exotic case.
B – Individual acknowledgement with document
The forklift driver returns the putaway document after putaway; this document is used for posting. In manual picking warehouses, the employee confirms the putaway via MDT.
C – Online acknowledgement at the compartment This requires the industrial trucks to be equipped with wireless terminals
. Storage with an automatic storage and retrieval machine is logically equivalent to this case.
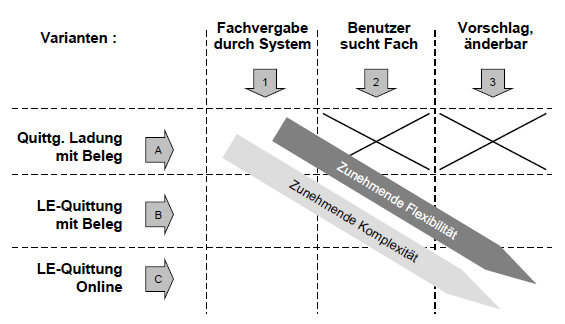
In addition, there are various ways of assigning compartments:
- Compartment allocation by the system assumes that the system knows all the data and decision criteria and that no constellations arise that cannot be physically implemented, for example (e.g. pallet higher/wider than compartment).
- The selection of the storage compartment by the user avoids this problem and thus lowers the requirement profile for data quality (and quantity).
- The combination of the first two variants is formed by a system proposal for the storage compartment that can be changed by the user.
In addition to the core function of searching for a free storage compartment, a modern logistics system can also take over the assignment of a forklift (see forklift guidance system).
Inventory that is urgently required for shipping is intercepted directly at goods receipt via “cross docking” and forwarded directly to goods issue, bypassing the actual warehouse. In some cases, bypass deliveries can also be made to this area if there is an urgent requirement in order picking.
Summary of the putaway process in intralogistics
The process steps that are carried out during putaway include
- Accept transport order
- Identify article
- Pick up articles
- Transporting items
- Storing items in the warehouse
Short throughput times, high process quality and flexibility in putaway are among the goals of this business process.
A quality check often takes place between the goods receipt and putaway processes. If the quality meets the relevant standards, the item is released for use and booked out with a subsequent inspection document. This is followed by labeling and any special processes, such as repackaging an item. When orders are accepted, they are usually allocated via mobile data capture (MDC). The destination is then assigned automatically. Scanning a barcode on the item enables exact identification, whereupon the items are either picked up manually or automatically transported to the warehouse using materials handling technology. A suitable storage location is identified, the items are placed there and the transport order is completed. Once storage has been completed, it is possible to clearly assign items and storage locations using item barcodes and shelf barcodes.
From this process, the number of putaways, the number and distance of storage locations and the number of items are important for the control center.
The number of putaways, capacity utilization, putaway time, work progress and the quality of the putaway all play a role in measuring the targets.
Further information: