Project report of a modernization for an innovative power tool manufacturer
In order to take into account the rapidly developing new possibilities of digitalization, a leading global manufacturer of power tools decided to modernize its warehouse located in Rhineland-Palatinate. Dabei standen sowohl das Lagerverwaltungssystem als auch dessen angegliederte IT-Systeme im Fokus. Der Standort realisiert einen wesentlichen Teil des weltweiten Umsatzes der Eigenmarke des Herstellers von Heimwerker- sowie Profiwerkzeug. Betrieben wird das Warehouse über einen Logistikdienstleister. Auf 80.000 m² bearbeiten 850 Mitarbeiter eine Kapazität von etwa 150.000 Paletten. Das Distributionszentrum zeichnet sich durch vollautomatisierte Hochregallager und komplexe logistische Prozesse aus. In einem gemeinsamen Projekt zwischen dem Elektrowerkzeugproduzenten, dessen Logistikdienstleister, TUP sowie SSI Schäfer sollte unter Volllastbetrieb die bestehende Lösung durch ein modernes Warehouse-Management-System ersetzt werden. Eine Aufgabe, wie gemacht für die Retrofit-Experten des Software-Unternehmens aus Stutensee.
The initial situation of the project
Within the warehouse, orders were processed via a complex IT landscape with a large number of interfaces provided by several software suppliers. The high level of automation causes the additional challenge throughout the project that many trades, processing types and their respective dependencies must be taken into account. Due to the fluctuating customer order volume with high order peaks, a key requirement for TUP was and still is that the changeover should take place in all areas during ongoing operations – without generating negative effects on the delivery fulfillment of the tool manufacturer’s end customers. The project, which began in 2019, aims to replace the diverse software landscape step by step by 2024 under a TUP solution developed specifically for the site. Sub-projects, also referred to as “Migs” for migration by the teams, will take place in this order: Loading, goods receipt, delivery, special processes.
Parallel operation with "rotary control" during migration steps
During the first Corona phase in 2020, DIY stores recorded huge sales. According to the absatzwirtschaft.de platform, it was the most successful spring quarter in the company’s history for Hornbach, for example. For the DIY stores, the Rhineland-Palatinate warehouse represents a hub for the consolidation of products delivered from all over the world. Thus, for the intralogistics project, this meant that the migration had to run absolutely smoothly in order to fully exploit the potential of this situation.
In the first migration stage, which has already been successfully completed, the systems required for loading shippable goods, outgoing goods, and customs and dangerous goods handling were transferred to fine-tuned parallel operation. The exchange between the legacy and new systems was performed through a high-performance interface to ensure that both could take on the full load at any given time. This approach ensures that the fallback solution is a constantly available and, above all, arbitrarily loadable part of the migration. During the first stage, for example, it was possible to decide per individual truck which system should take over the handling. For the following migration steps, decisions are made together with the power tool manufacturer’s teams as to where and how the rotary control principle should be applied in order to ensure delivery capability in all cases.
This approach proved particularly successful in project implementation under pandemic conditions. The teams on site were able to react flexibly to emerging staff gaps and changing demands on the new system by distributing accruing order loads between the old and new systems depending on the situation. In the second migration step, the same principle was used to transfer the goods receipt and quality assurance processes. The immediately following stages of the project include the control system for industrial trucks, order dispatching and order picking. Here, the focus will be on process optimization through routing and digital support in the picking processes.
The substructure of software architecture and efficient test solutions
To identify project risks and still be able to perform comprehensive tests during operation, the TUP team relied on the principle of hexagonal architecture and lean test programs. These systems mimic the actual live systems – such as enterprise resource planning (ERP) or the material flow computer – only to the extent required for the test scenario. The decisive advantage is that a functional test requires significantly less coordination and planning effort, and the solutions, which are also referred to as “imposter systems” by TUP, are easy to parameterize and adapt. For example, communication can be tested at the ERP level, even if it is still in the design or early development phase. This reduces the dependencies between the trades, which reduces project risk and enables detailed testing.
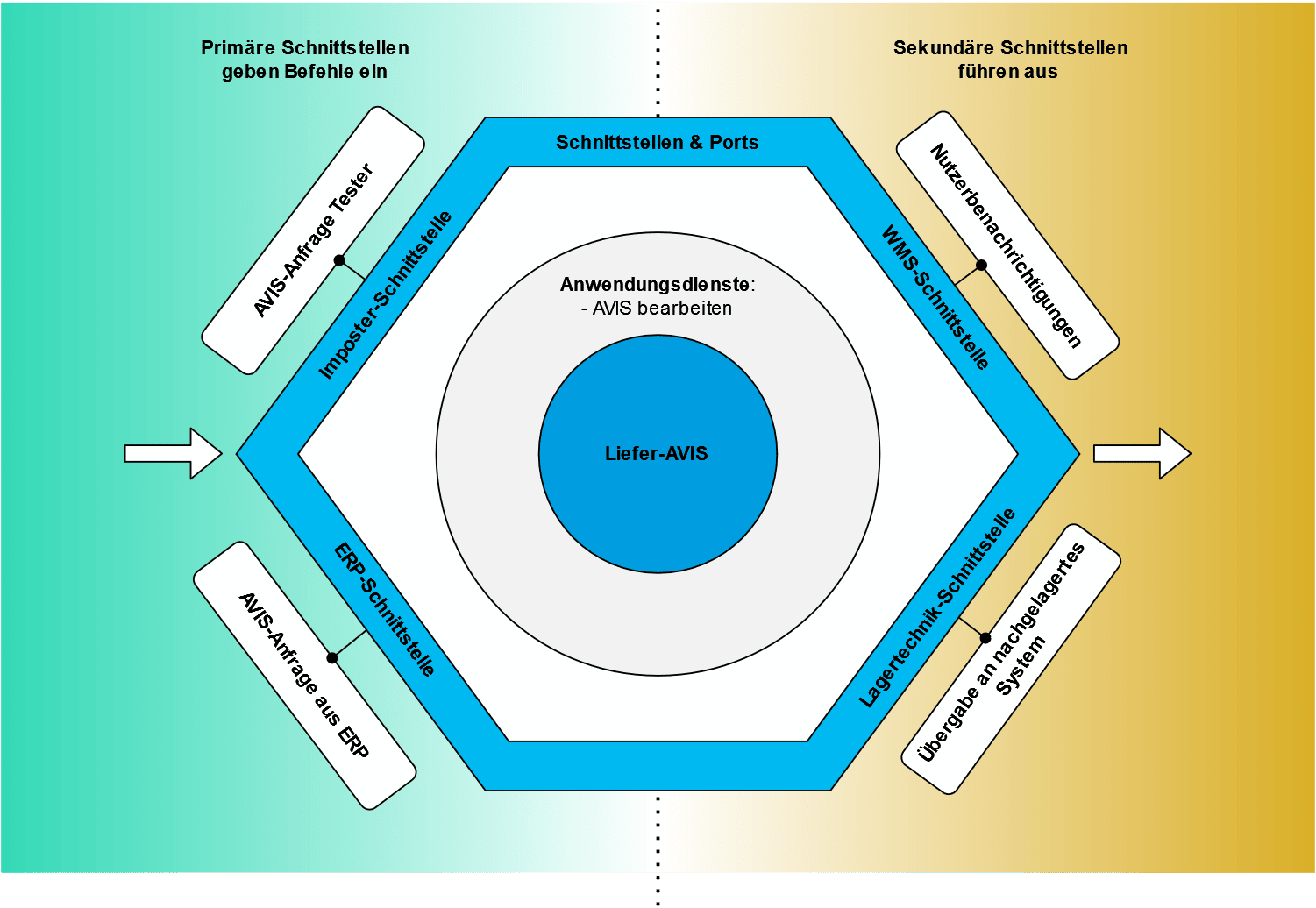
The central aspect of the hexagonal architecture already mentioned is the separation of the domain-oriented modules from their technical requirements. This results in powerful interface concepts that enable the exchange of connected elements, such as inventory and test systems or user interfaces, at any time.
Cross-company project teams instead of customer-service provider relationships
The complex mix of many highly automated solutions and several software suppliers, combined with the simultaneous requirement not to impair the site’s performance, necessitated and still necessitates cross-company collaboration between all project participants. Teamwork was and is a key success factor. In this context, the partners use the “arc42” model for planning software architectures. It is a pragmatic template for developing, documenting and communicating software architectures with many different stakeholders.
The “arc42” model presents structures, overarching concepts as well as justifications of joint decisions in a generally understandable way. It prevents a patchwork of problem-solving approaches from developing and individual project participants from being out of touch at some point. It also prevents the documentation from being too much from a software perspective and becoming difficult for logisticians to follow. On the basis of “arc42”, cooperation between all participants at eye level for constructive solution finding is feasible across companies and, above all, in the long term.
Avoid Big Bangs in complex projects
This type of cooperation also forms the basis for successfully implementing a solution like the “Drehregler”. This is because a sophisticated migration concept and individual software solutions are needed in the background. The advantage compared to so-called big bangs, which are often used when ongoing operations are not to be affected or are to be affected only slightly, is a decided minimization of risk.
After all, in complex software projects, no one can predict with absolute probability what will actually happen as soon as the switch is flipped during a Big Bang. The opposite approach is phased migration, in which specifications, tests and the respective commissioning of individual stages are implemented together. In this way, unpleasant surprises can either be avoided completely or at least isolated immediately and remedied promptly.
Sources and links
Sources
Additional links