When it comes to constructing a new building or expanding a warehouse, storage-consolidating solutions such as cube storage systems or automatic small parts warehouses (ASRS) are often chosen modules. The advantages are obvious: the space-saving designs enable flexible optimization of intralogistics processes in a wide range of industries. They allow for highly efficient use of space, and the additional automation increases resilience in times of a shortage of skilled workers in the warehouse.
However, in addition to the physical key figures, the software side must also be taken into account when integrating systems that can be described as “black boxes” – whether they are compact bin systems, automated small parts warehouses, shuttles, paternosters, etc. The new investment must be integrated into the IT infrastructure in line with the company’s requirements. This article discusses the integration using middleware and compares this approach with a direct connection to a warehouse management system (WMS).
What are the special features of these storage consolidation systems?
Manufacturers of such systems, such as AutoStore, offer their own software and hardware components for simple, usually stand-alone operation. In addition, there are specialized service providers who, as integrators, offer the connection to various WMS and ERP solutions for use in more complex warehouse environments.
The promise here, in addition to cost-effective integration, is that the insights gained in various industries will be incorporated centrally into the updates to the systems, and that the combined experience can thus be used for the benefit of the company. The disadvantage is that this sets clear limits to the flexible adaptation to your own processes. If, on the one hand, it is possible to intervene in the aforementioned systems to a sufficient extent, this costs a lot of money in the vast majority of cases.
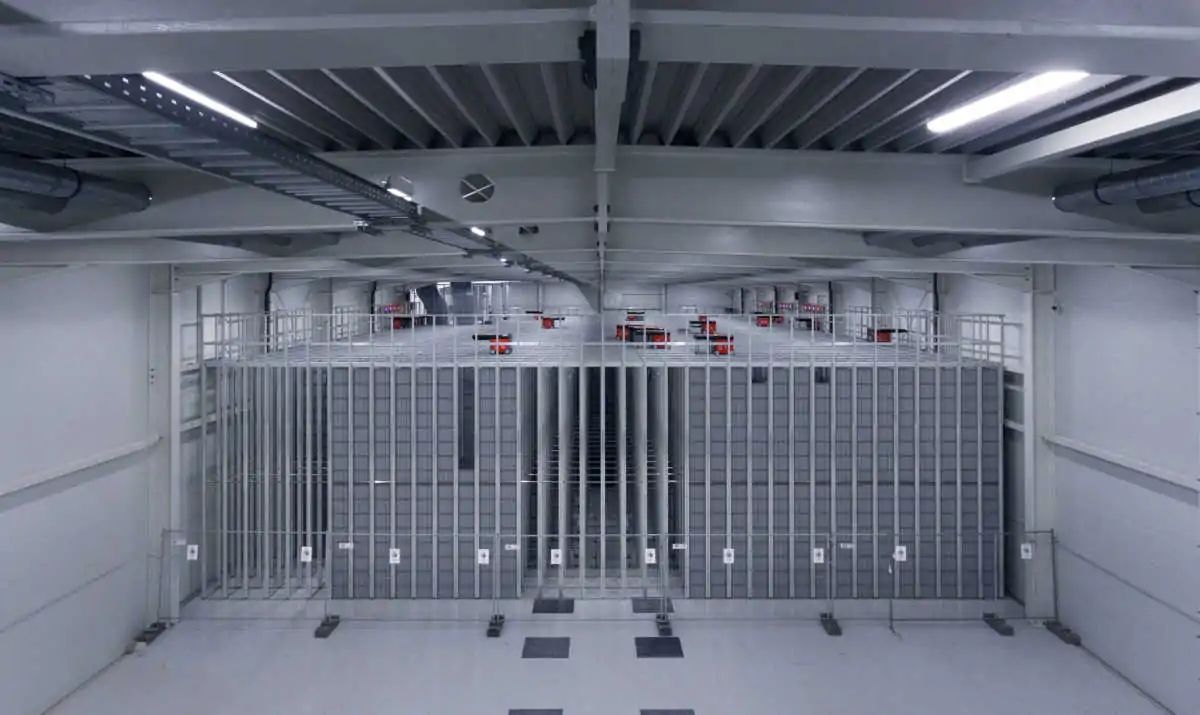
In addition to cost advantages, proprietary hardware-specific systems promise a high degree of stability and standardization. However, these aspects often only come into play if companies and their processes are closely aligned with these standards. In turn, the dependency on the manufacturer is often underestimated, both in terms of adaptations and long-term product support. Not only Silicon Valley giants, such as Apple, pursue the strategy of the “walled garden”, in which the product world is sealed off from the outside as much as possible in order to retain customers in the long term.
It is therefore essential to consider the strategic goals of the company: If you want to be able to react flexibly to market changes, systems that specify processes with a high degree of standardization may be a hindrance: the ability to adapt to new circumstances and the speed of implementation are always dependent on actors with their own priorities and, above all, processes. [/vc_custom_heading]
To prevent the Cube storage solution or the automatic small parts warehouse from standing as a lonely island in the middle of the respective intralogistics landscape, they must be connected to the existing processes and the IT infrastructure. At the warehouse level, in most cases these are enterprise resource planning solutions (ERP), warehouse management systems (WMS) and material flow control using material flow computers (MFC) or warehouse control systems (WCS).This is the fork in the road where a warehouse operator has to decide: should the […] The decision should be based on the existing IT design of the company’s own intralogistics. Only in this way can smooth integration and, above all, long-term efficiency be guaranteed.
How is the IT landscape set up?
To make a well-informed decision, it is essential to have a realistic picture of your own IT. Do you have systems with a granular update capability that can be updated and modified independently of each other, or are they software monoliths that have to be extended via version releases? What is in your own hands and what is in the hands of third parties? A company’s IT landscape is crucial for the choice of integration strategy. An IT landscape designed for your own needs offers flexibility to efficiently implement specific requirements, while purchased monoliths are proven solutions for standard scenarios, but offer fewer customization options, which often becomes apparent in small details: A standard parameter that generates disproportionate effort because it has to transmit more or different information. Often, a slow obsolescence of the monolith can also be observed because people are afraid of interfering with the running system and the change would be a risky major project based on the big bang principle.
Middleware vs. direct integration into the WMS
What is initially attractive about middleware is that responsibilities are clearly defined. The provider is contractually responsible for the functioning communication between the cube storage system and the warehouse management system. Since, as described, the schema of the respective integrator or service provider goes along with it, a clear, moderate cost point also tends to be the first to appear, even before the desire for customization.
But the price for this supposed security in terms of costs and responsibility is paid elsewhere: the network of dependencies on third parties and the more complex communication of three instead of two instances, with their own requirements for data management, maintenance and IT infrastructure, reduces operational effectiveness and adaptability.
The system’s intelligence is also handed over to third parties: If a WMS can only transmit orders, the decision on how to execute them lies with the middleware. This results in a potential optimization gap: Even if a WMS is perfectly adapted to your own needs, intermediary instances may not be, because they can either not be adapted at all or only with difficulty. If, on the other hand, a WMS is able to control automation solutions such as a cube storage system directly, it is possible to store and retrieve goods in a process-optimized manner based on an overall perspective.
It is already becoming apparent that this variant also entails requirements for the warehouse management system (WMS) in question. Of course, a corresponding adaptability must first be supported by the warehouse system in use. Accordingly, the prerequisite for direct integration into the WMS/WMS is the flexibility of the said system itself. Since there are sometimes major differences between the software systems of different providers, this option is sometimes overlooked when purchasing automated storage systems. However, with the right warehouse management system, storage systems that were designed for use as a stand-alone solution can also be directly integrated. Compared to the use of middleware, this avoids additional complexity in the IT infrastructure due to the necessary systems, double data management and an additional system layer. It also eliminates the need for a higher level of coordination with the middleware provider.
However, if you want to have the greatest possible freedom to interpret and adapt your own processes, you also need to be aware of the basic requirements for doing so: the will to continuously optimize along the entire process chain and the ability to integrate all domain experts into the project transparently and on an equal footing. Instead of a system within a system, an integrated, hierarchically clearly defined warehouse management system with clear decision-making authority can be used for smart control: if the WMS can not only specify what is to be outsourced, but also how this is to be done in a process-optimized manner, the Cube Storage system can fulfill this order in a targeted manner. If such an interaction is in place, it can enormously enhance the warehouse as an efficiency multiplier.
Our outlook
The choice between a direct connection to the WMS or the route via middleware depends on the specific requirements and conditions of the company. From an operational perspective, the direct connection is ideal: performance, data and interpretation sovereignty are in one system, which directly and optimally fits the cube storage solution into the process world, controls it. However, the prerequisite for this is the corresponding corporate culture, in which process optimization is the focus and the domain experts are involved early and comprehensively. As mentioned, the possibility of mapping in individual WMS in particular is sometimes overlooked, and thus the full spectrum of integration options is considered. In addition, there are aspects such as apparently low acquisition costs and externalization of responsibility – supposed advantages that in many cases, however, are later paid for in hidden ways due to the optimization potential that has been awarded and the associated opportunity costs. From an operational point of view, direct integration welds domain experts together into interdisciplinary teams and enables continuous improvement during operation, since lengthy release cycles are eliminated. In the long term, lean IT also results in greater cost advantages. Depending on the rate of growth, the Tower of Babel of languages can quickly arise when various intermediate middleware solutions communicate with a warehouse management system in intralogistics. In our view, a clear, lean IT architecture that can keep pace with the growth of the company is crucial for long-term success.