AutoStore is a Norwegian storage technology and, according to the company of the same name, is particularly suitable for use as an automatic small parts warehouse. The storage system does not use traditional shelves; instead, it uses modular containers that are stacked on top of each other within an aluminum structure and moved by robots. AutoStore technology is basically an all-in-one solution consisting of goods receipt, putaway, warehousing, picking, packing, and goods issue/shipping.
AutoStore and Cube Storage – What’s the difference?
AutoStore is both a product name and the name of the corresponding company. Cube storage and cube storage automation, on the other hand, refer to the technology and the principle in general. However, it is fair to say that AutoStore, although a relatively new brand, is considered a generic name. Just as “Kleenex” is used not only to refer to paper handkerchiefs of that brand, but to paper handkerchiefs in general in English-speaking countries. The English-language equivalent of the german “Tempo” is “Kleenex”. Cube Storage is a space-saving, automated storage system that follows a cube principle. This makes use of all the available space in a warehouse. With its invention of the same name and over 1600 patents, Autostore pioneered its field and established Cube Storage Automation in modern logistics.
The robot-based storage and picking solution AutoStore is specifically aimed at projects that are usually designed to save space; often, such a system is installed in an existing building/project to reorganize an existing warehouse section and the automate work steps in the course of digitization – these are usually small project solutions in which, for example, the routes of employees within a picking zone are to be optimized: Each manual AutoStore workstation describes the goods-to-person picking method.
Advantages and disadvantages of the AutoStore system
Advantages
- High utilization of space and volume
- 24-hour operation is possible
- Compact storage
- High level of automation
- Theft protection (closed system)
- Picking stations can be freely placed around the AutoStore system
- According to the company, energy savings of over 90 percent can be achieved compared to conventional solutions with storage and retrieval machines
- It is possible to expand capacity and speed during operation
- Low personnel costs because only picking stations are operated by staff
Disadvantages
- Goods are limited to the permissible container mass (maximum 35 kilograms).
- High investment costs.
- Regular / ongoing maintenance by staff
- Can only be used for simple logistics processes
Structure: Cube Storage
- Container racks made of aluminum, also known as grids
- Containers, also known as bins, which are available in different depths and heights
- Shuttle vehicles, also known as robots
- Picking modules, also known as ports. These can be placed anywhere on the container rack (grid)
Editor’s note: To ensure that the desired goods can be accessed quickly, fast-moving items are stored in the upper part of the stack, while slow-moving items are stored in the lower part. In general, thanks to the design, the goods are handled according to the LIFO principle; however, there are also systems that now support FIFO (see link to LIFO); the focus here is on a constant relocation of goods, controlled by the warehouse management system.
Materialflusssysteme / Fördermittel- und Lagertechnik / 4th edition / Michael ten Hompel, Thorsten Schmidt, Johannes Dregger / Page 72 / Kleinteilelager via AutoStore
Technical element: Cube Storage Shuttle (Robot)
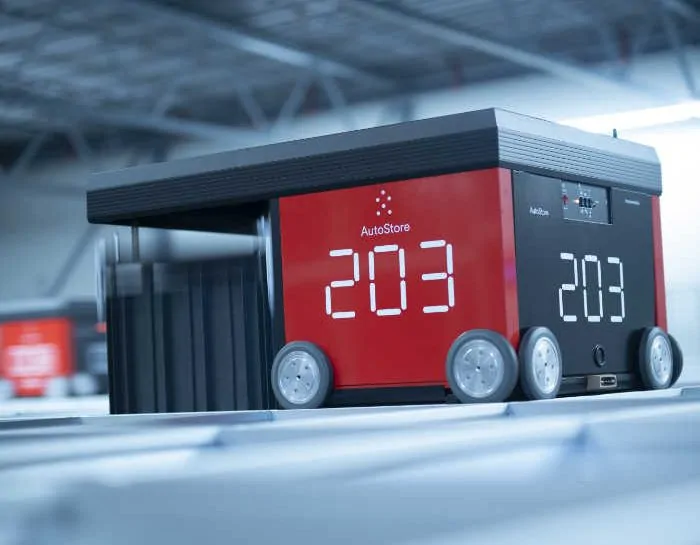
From a technical point of view, robots are conventional shuttle vehicles, but the storage and retrieval processes are carried out in a vertical form; the containers are accessed by lowering a special gripper device. A robot is battery-powered and guided by a specially programmed routing software (material flow computer or warehouse management) on the grid. A robot supports four directions (forward, backward, right, left); it rests with its eight wheels, two on each side (see photo), in rails. In practice, the robot picks up the target container, also called a bin, and takes it to the desired picking location (port), where the goods and bin are lowered to the picking location. Communication between the systems involved (warehouse management system, material flow computer, host system, shipping system) usually takes place via the local network, while the robots are controlled via a radio connection.
Technical element: The Cube Storage warehouse structure (grid)
The robots described above move on a rail grid construction. Each square provides space for several bins, which are firmly integrated into the aluminum structure and appear as rectangular cells on the grid. Although the grid can vary in shape and height, it is limited to a height of 5.4 meters and has a storage capacity of between 2,000 and 200,000 bins per system.
Technical element: Cube Storage bin
The transport unit is called a bin and can be used in different materials and sizes depending on the project. What is special about it is the design itself; the bins are stacked on top of each other without spaces in between. According to the manufacturer, it is even possible to adapt the AutoStore installation (the grid) to individual storage situations – as an example, support columns and common warehouse obstacles are mentioned. Such a container can have a volume between 48 and 75 liters and a maximum load of up to 35 kilograms.
Technical element: Cube Storage picking workstation (port)
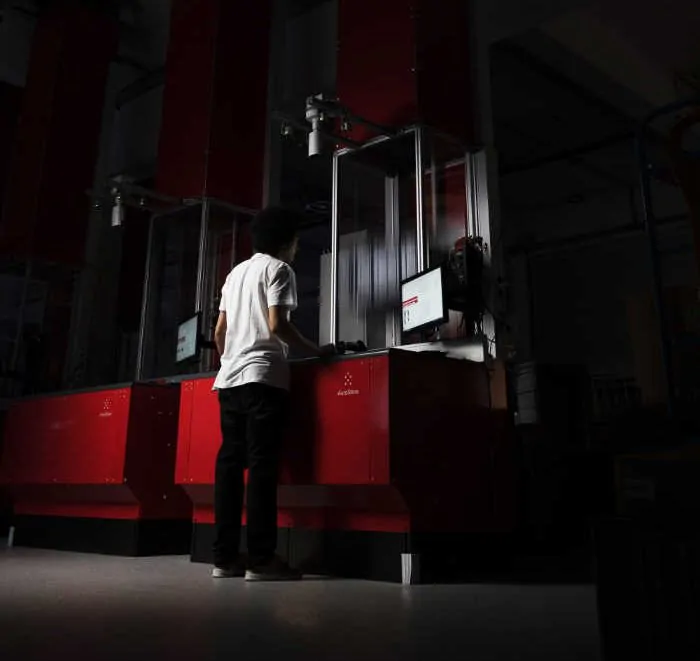
AutoStore uses the term “port” to describe the classic picking workstation. This can be positioned anywhere on the AutoStore system sides and is supplied with bins and thus goods by the robots. Once the desired goods have been picked in the specified quantity, the bin is picked up again by the robot and put away. The storage location can now be redefined by the warehouse management system based on inventory management parameters and the current order volume.
It is already possible to have unmanned warehouses, especially in inbound logistics, with full load carriers – when it comes to simple processes. Companies with complex picking processes and a high number of variants, see range of products, cannot do without staff-based labor.
Logistik Heute
System performance of an AutoStore system
The picking performance of an AutoStore system is 180 – 500 items per hour / 120 – 500 bins per work station. As a rule, at an acceleration of 0.8 m/s2 and a speed of 3.1 m/s, approximately 25 storage or retrieval operations per robotic unit are handled per hour. Up to 120 robots have to be moved to achieve an average of 2,000 storage or retrieval operations*.
An AutoStore system can therefore also be very expensive and unprofitable. By way of comparison: a large distribution center, such as in the fashion industry (shoes, clothing, accessories – excluding (hanging) pocket sorter goods) can process several thousand items per hour with fewer than 50 people. However, this significant difference in performance is based on the respective alignment of the storage system used. While a wide area is often used in distribution centers, this strategy is avoided with AutoStore. The variety of products is also usually a deciding factor in which storage system is chosen. For example, if there is a high range of products, a classic storage topology with manual picking processes (see two-stage picking) is preferred. On the other hand, if the range of products is small, a storage system with a high degree of volume utilization and automation comes out on top – for example, the AutoStore system.
Summary of the Cube Storage (Autostore) system
The AutoStore system is particularly suitable for simple logistical warehouse processes. It is usually highly automated and designed for small parts (small assortment). It consists of the storage construct (grid), the bins, the shuttles (robots) and the picking workstations (ports).
*Hoermann Logistik AutoStore Flyer
Image rights: AutoStore