Coded information can be stored in many different ways. In addition to mechanical, magnetic and electronic storage, a conventional type of storage has also become established, not least due to the further development of optical reading systems – the barcode. Barcodes are based on the binary principle, which is represented by a certain number of wide and narrow parallel bars and spaces. There are various barcodes that differ in their form of representation (number and width of the bars). The sequence of this structure results in a defined numeric or alphanumeric statement. This type of data provision is often superior to other systems, particularly in the transport and storage sector, where many different items are labeled and managed.
Structure of a barcode and advantages of barcode systems
A barcode is divided into different areas: The quiet zones are unprinted areas before and after the actual barcode. They are usually white. The following rule of thumb applies to the width of these zones:
- at least five times the widest bar (Datalogic, a scanner manufacturer)
- at least ten times the narrowest line (SICK, a sensor manufacturer)
The start character (start margin) is a special dash/gap combination. It is always at the first position of the code. When this character is recognized, the decoder begins to process the scanner’s signal stream. The start character is also used for security purposes. It signals to the system that a barcode symbol is actually being received and not some sequence of reflected extraneous light. The stop character (stop margin) is also a serial character. It signals the end of the code. The decoder is thus informed that the complete code has been received, checks and translates the message. To ensure that a code can be read from both sides, the start and stop characters are not symmetrical. If the code is read from the “wrong” direction, the decoder recognizes this and converts the character string internally. The message contains the actual information. The code type determines the syntax. The check digit (checksum) is an optional character and is defined for most code types. It is used to check the plausibility of the read code.
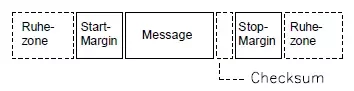
Barcode systems have numerous advantages, including the following:
- Fast capture
- Eliminates errors caused by keyboard input or data manipulation
- Flexible and fast creation of data carriers (labels)
- Cost-effective data storage medium
- Can be combined with plain text on one data carrier
Overview of different barcode types
There are a large number of different code types, some of which are also used on a manufacturer-specific basis. The four most important types for material flow systems in intralogistics are listed in the following table. These can be processed by most reading systems or decoders from different manufacturers and are therefore referred to as standard codes.
Standardcode | Informationsträger | Zeichenvorrat | Vor- und Nachteile |
---|---|---|---|
2/5 Industrial | Only the dashes (5 dashes = 1 character) | Digits 0-9 | + easy to read + easy to print - low information density (3.9 mm/digit with min. pitch 0.3 mm) |
2/5 Industrial | Dashes and gaps (5 dashes or 5 gaps = 1 character) | Digits 0-9 | + high information density (2.3 mm/digit at min. 0.3 mm) - low printing tolerances +/- 10% |
Code 39 | 5 dashes and 4 gaps per character (one wider gap = character spacing) | Numbers 0-9 Letters A-Z 7 Special characters | + alphanumeric display - low print tolerances +/- 10% - low information density (4.8 mm/digits with min. 0.3 mm pitch) |
Code 128 / EAN 128 | 3 bars and 3 spaces per character (1 character consists of 11 elements) Four-width code | ASCII character set | + alphanumeric display + high information density + high reading reliability - not widely used - high demands on printing technology |
Barcode label and barcode system
A barcode is usually scanned over the entire bar height. This results in multiple scans of the code. Problems mainly occur when the code is heavily soiled, damaged or in poor lighting conditions (insufficient/interfering light). However, the most common cause of reading errors is poor print quality of the barcode label. The better the print quality, the better and more reliable the readability of the code. This increases the first read rate and reduces the risk of incorrect reading due to substitution with a different bar/gap sequence.
In order to achieve the best possible legibility, the print on code labels should meet the following quality criteria:
- Compliance with the dimensions and tolerances in accordance with the code specifications
- If possible, no spots or gaps (a spot of a certain size in a gap is recognized by the scanner as a narrow element)
- Minimal edge roughness (the code lines should have edges that are as sharp and even as possible)
- High contrast ratio and sufficient reflectivity (good reading reliability with black lines on a white background)
Physical requirements for the label are:
- Good adhesion of the ink and the label
- Resistance to oil and chemicals
- Wear resistance
- As lightfast as possible (no yellowing)
Today, laser scanners or image processing cameras (CCD cameras) are usually used as readers. A minimum contrast between the bars and the background is necessary for error-free reading of a barcode so that the code can be recognized correctly. This contrast is a dimensionless quantity and has been defined as the print contrast signal (PCS) in accordance with DIN 66236.
The PCS is calculated using the following formula:

The best contrast is achieved with a white background and black strokes. In some cases, dark green or dark blue lines can be applied to a pastel-colored background . However, special red light illumination (e.g. laser scanner in the red range at 600 – 632 nm) is then required for reliable reading.
Basic elements of a barcode system
In addition to the scanner, other basic elements are required for handling barcodes in material flow systems. These elements are:
- The printer creating the barcode. The code is either printed directly onto the packaging or attached to the product or a transport aid.
- The sensor scanning the coded information optoelectronically. It receives the diffusely reflected light of the line/gap sequence and converts the light/dark sequence into electrical signals.
- The decoder (also reader) converting the electrical signals from the sensor into a digital pulse sequence and evaluates them using a microprocessor. The decoded characters can be displayed and made available for data transmission via a serial interface for the respective higher-level data processing system.
- The computer receives the transmitted data protocols, processes them independently or forwards them. Only relevant data for controlling the material flow is forwarded to the transport control system.
The code density of barcodes
The terms high-, medium- and low-density are often used in connection with code quality.
The code density is differentiated according to the minimum line width:
- Ultra High Density-Code (minimale Strichstärke < 0,19 mm)
- High Density-Code (minimale Strichstärke 0,19 mm – 0,24 mm)
- Medium Density-Code (minimale Strichstärke 0,24 mm – 0,30 mm)
- Low Density-Code (minimale Strichstärke 0,30 mm – 0,50 mm)
- Use at long distances (minimum line width – 0.50 mm)
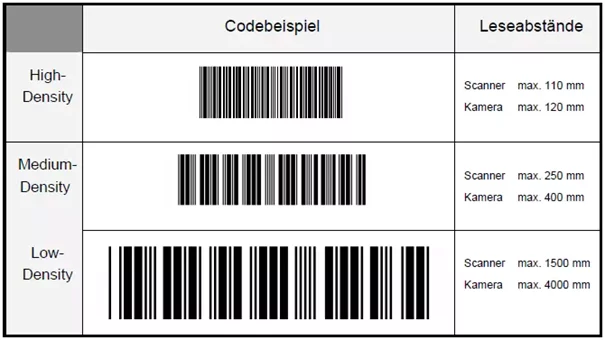
Together with the selected line width ratio, this results in a more or less high information density (character/inch or character/millimeter). Ultimately, the reading distance is decisive for the choice of line width.
Self-checking of barcodes
There are codes that can be checked due to their structure. Most barcodes have a so-called self-checking function to increase reading reliability. With this type of barcode, for example, the number of thin and thick bars per digit is the same or each character contains exactly 2 wide bars (so-called 2/5 codes). Due to this definition, a plausibility check is possible by simply counting the bars.
The use of a check digit (checksum) makes the reading even more reliable. The check digit is represented by an additional digit immediately before the stop character of the code. If this read check digit does not match the digit calculated by the decoder, the code will not be transmitted.
Check digit calculation according to modulo 10
Modulo 10 is a widely used method for checking identification numbers.
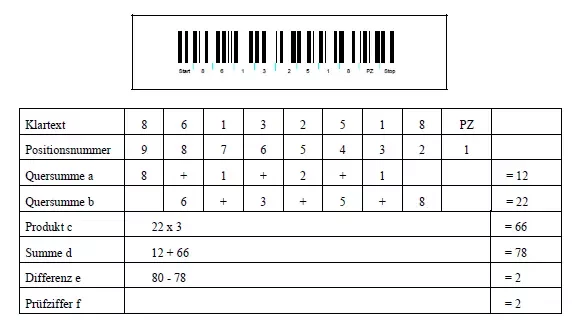
- Sum of all digits with an odd position number
- Sum of all digits with an even position number
- Multiplication b by the factor 3
- Sum a + c
- Difference from d to the next multiple of 10
- The result e is the check digit PZ
Barcode terminology
The important elements and terms in connection with barcodes:
- Bars: Dark elements of a barcode.
- Gaps: Bright elements of a barcode.
- Barcode: A defined number of parallel, alternating bars and spaces.
- Start and stop characters: Each code begins with a start character and ends with a stop character. The start and stop characters can also be used to determine the code type.
- Discrete code: A barcode that is only formed from bars of different thicknesses. The gaps are the same width and contain no information (e.g. 2/5 industrial).
- Continuous code: In addition to the bars of different widths, the gaps of different widths are also used as information carriers (e.g. 2/5 interleaved).
- Quiet zone: Unprinted free space in front of the start and behind the stop sign. This zone is necessary to signal the start and end of the code to the reader.
- Self-checking code: Enables independent detection of errors during reading, according to a predefined algorithm. However, substitution errors cannot be completely ruled out.
- Bar width ratio: Ratio of wide bar (gap) to narrow bar (gap) in a code.
Barcode standards - EAN, GTIN and GS1-S
The most widely used barcode is the EAN code (European Article Number), which was designed in 1976 for the European food trade. The aim of the EAN was to ensure the unique identification of inventories throughout Europe. After just a few years, EAN coding was also used in Asia, Africa, Australia and South America. In 2002, the globally active umbrella organization EAN was merged with the North American UCC (Uniform Code Council) to form today’s GS1 (Global Standards 1). As a result, a new term was to be established for the compatible EAN and UPC (Uniform Product Code) identification systems: GTIN (Global Trade Item Number). GS1 hopes that this will lead to a globally unique identification of articles and services.
The GS1 standard
The GS1 standard is already an integral part of the value chain during production. During the procurement and manufacture of products, each individual item and the product itself is given a Global Trade Item Number, or GTIN for short (unique item number). This is followed by information for further processes such as storage, transportation, delivery, trade and return. As a rule, they are all stored together on the code variant “GS1 standard 128“. Each item is thus given a unique label that identifies it within a specific packaging hierarchy.
The individual data element generally consists of the two- to four-digit data identifier (see graphic) and the subsequent data content, for example the best-before date. In addition to the batch number and the expiration date mentioned above, it can also store the item description, transport unit, identification and classification number, batch number and net weight.
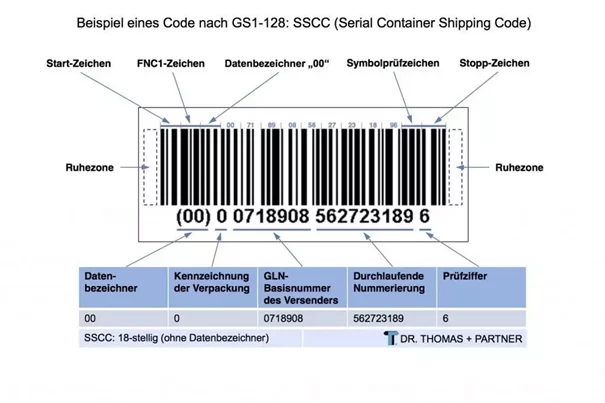
Advantages of the GS1 standard:
- Fast data scanning at goods receipt or in the middle of the goods flow
- Flexible and fast creation of data carriers and labels
- Cost-effective data carrier medium
- Can be combined with plain text on one data carrier
- 16,000 or more scans per second, at a conveyor speed of 2.3 meters per second
- Verifiable error-free barcode capture Fewer manual processes, but more automation
- Data reconciliation at a scanning station in real-time
Comparison of RFID and barcodes in operation in the retail sector
The marking of a product with a barcode has become established for the automatic identification of inventories in retail. Compared to other possible identification methods, barcodes are inexpensive, reliable and easy to produce. The RFID chip is deemed by some to be the successor to the conventional barcode. Both technologies are compared in the following table.
Parameter | Barcode | RFID |
---|---|---|
Typical data volume | 1 to 100 bits | 16 to 64 kilobits |
Data access | "Write-Once" + "Read-Only" | "Read-Only" / "Read and Write" |
Communication direction | one way | bidirectional |
Data transmission | optical | Radio transmission in the HF, VHF or UHF range |
Max. Distance between data carrier and reader | 0-5 m with line of sight | 0-100 m without line of sight, strongly dependent on frequency and power supply |
Technical disruptive factors | Soiling, damage, optical cover | Interference of radio transmission by metals and liquids |
Bulk detection | not possible | possible |
Read confirmation | yes | no |
Multiple descriptions of data | not possible | possible |
Theft protection | not possible | possible |
Marking costs | low | medium/hight |
As can be seen from the table, there are some limitations to barcode technology that do not apply to RFID technology. Accordingly, RFID systems are superior to barcode technology (which is described in detail in another article). This mainly relates to the advantageous storage options and factors that have to do with environmental influences. These include, for example, dirt, moisture and optical covers.
In addition to the functionalities of RFID, the focus in stationary retail is on economic efficiency. The disadvantages of RFID transponders compared to barcodes are the higher costs and the investment required for the necessary hardware and software for RFID systems.
Summary
Barcodes are binary codes consisting of an array of parallel bars and spaces. These are arranged according to a predetermined pattern and are interpreted as a specific character or character sequence. They can be read using a laser scanner. The different reflections of a laser beam on the black lines and white gaps are evaluated. The reading can also be carried out using a CCD (charge-coupled device) reader. The CCD reader is designed like a barcode camera with a CCD line. The code is displayed and evaluated with sufficient contrast on the CCD line.
The development of barcode reading systems and improved label printing technology have made it possible to label any product or conveyor aid and achieve targeted control of the material flow via the assigned number (order or item number). Today, the state of the art is that product data can be scanned in bar-coded form with a read rate of up to 500 scans/sec. as it passes by. With the appropriate lenses, a depth of field of up to 1500 mm is possible.
Processing the data with the computer systems available today enables flexible control of transport and storage orders. In conjunction with a database, the production volume can be called up at any time. Each completed work step is documented. Barcodes are used worldwide in different variants and international standards. They have established themselves as a very practical method of labeling item numbers. In some cases, however, barcodes are being replaced by RFID technology.
Other articles that may also be of interest to you:
Two-dimensional codes