Supply-Chain-Simulation
The general aim of supply chain simulation is to analyze the dynamic behavior of complex value chains, taking into account stochastic influences such as forecasting errors, production, transport and replenishment times. Central evaluation parameters are delivery service levels, costs and inventories.
Areas of application for supply chain simulation
In contrast to “classic” material flow simulation, e.g. the simulation of a production plant in the automotive industry or a logistics system, the location is the smallest unit in a supply chain simulation. This means that production resources (e.g. conveyor technology) and intralogistics elements and processes are not mapped in detail. In contrast, the information and planning processes (including the planning and forecasting procedures) are the central focus of this type of simulation.
The main areas of application for supply chain simulation are support for network design and master planning for procurement, production and distribution (e.g. parameterization of planning processes). At the network design level, planning processes are mainly used with the support of aggregated optimization models. At this level, issues such as location decisions or article allocations can be processed with comparatively little data input.
At the master planning level, i.e. when it comes to planning material flows, procurement strategies or distribution, the event-oriented simulation of supply chains shows its strengths. Simulation enables the objective comparison of different network design variants based on their structure (e.g. for distribution networks), as well as their production and sourcing strategies. The influence of individual network parameters on the performance of the entire supply chain can be examined and evaluated in the course of network configuration.
This can include dimensioning inventory ranges and production resources, determining suitable transportation solutions (optimal means of transport, order cycles and quantities, etc.) or determining the optimal number of containers.
In general, simulation helps to identify interdependencies in complex networks that are difficult or impossible to find using static analyses.
Modeling approach and architecture
There are two modeling approaches with regard to software tools for simulating supply chains: 1. direct modeling in the simulator (including data storage); 2. generic modeling approach based on the separation of simulation model (building blocks) and data. In the first case, the model including all associated data is created in the programming environment provided by the simulator used. This has the disadvantage that the reusability of the model is limited and that the creation of different scenarios in a model is difficult or associated with redundancies in the modeling. The generic modeling approach avoids these disadvantages.
In the generic approach, the tool typically consists of three components: a graphical user interface with which simulations can be set up and executed and simulation results can be visualized; a classic database in which the data describing the supply chain to be simulated is stored; and finally a simulation engine with which the simulations are executed and results are generated.
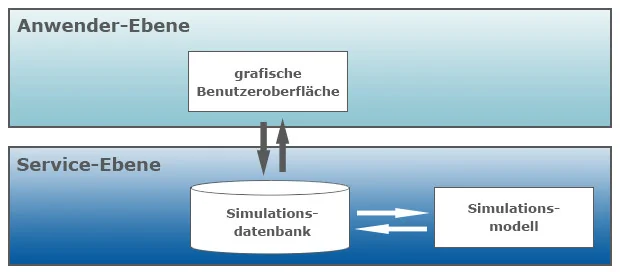
A key aspect of supply chain simulation is the large amount of data that can be generated in this type of project. This applies both to the procurement and to the preparation and processing of the data in order to make it usable for the simulation. The success of a supply chain simulation tool depends heavily on how the user is supported when working with large amounts of data. Assistance and import functions significantly reduce the effort required to create models. Combined with consistency checks when entering data, they form the basis for successful work in event-oriented simulation.
In general, the analysis and dynamic consideration of supply chains is becoming increasingly important, especially where the requirements of a supply chain can change dramatically within a very short time and corresponding solutions need to be developed quickly. Simulation is an ideal tool for providing reliable answers to the questions that arise when designing supply chains.
Further information on simulations can be found under Virtual commissioning.
Image source: Simplan AG