In this interview series, we talk to employees of the GRASS Group about the cooperation in the Hohenems central distribution center project. In the third part of the four-part series, Rene Malojer takes the floor, whom his path has led from starting as a working student to the position of head of the central distribution center in Hohenems.
What is your position and area of responsibility at GRASS?
My name is Rene Malojer, I have been with GRASS since 2013. Currently I am responsible for the central distribution center at the Hohenems site. I started in strategic logistics in my part-time studies, then my journey took me to site logistics, head of site logistics, head of dispatch control and finally to head of the central distribution center in Hohenems since May 2021.
So you have moved through several departments and different perspectives?
I have a classic background in project management, then I took over responsibility for personnel at the site and specialized in order-to-cash processes in the order center with the question of “How do the orders come in? Now I deal with the operational processes in the warehouse: incoming and outgoing goods, order picking, as well as the customs issues that arise.
When and how did you join the Hohenems project?
That depends on how you define the project timeframe. It has accompanied me already after the first year at GRASS. In 2014, we had to rethink the decentralized warehouse structure and answer the question of where the journey should go: How should we position ourselves in the future? How do we implement the results of the initial make-or-buy analysis? What should the flow of goods look like and where should the new warehouse be located? Basically, I was there from the early conceptual phase.
How was the cooperation with TUP from a personal and professional point of view?
At the beginning, there was a change of project members on both sides, which initially hampered the daily project business somewhat. However, this was quickly resolved on both sides and also led to a very good interpersonal relationship. We were able to communicate quickly at eye level and both sides gained valuable sparring partners: On the one hand, we from GRASS, who brought the experience from the past to the table, and on the other hand, TUP, a company that had implemented comparable projects and also was on the cutting edge in terms of requirements and implementation possibilities. So we had a very good partner on a personal and professional level during the project phase and also afterwards.
Was there a situation in which the process knowledge of GRASS and the market perspective of TUP have come together particularly well?.
Very specifically in order picking, I would say. The area is a hybrid system where picks are displayed on the screen and on smart devices. The source and destination pallets are also displayed and the employee is guided to them intuitively. This is where this experience of GRASS and the perspective of TUP have merged ideally.
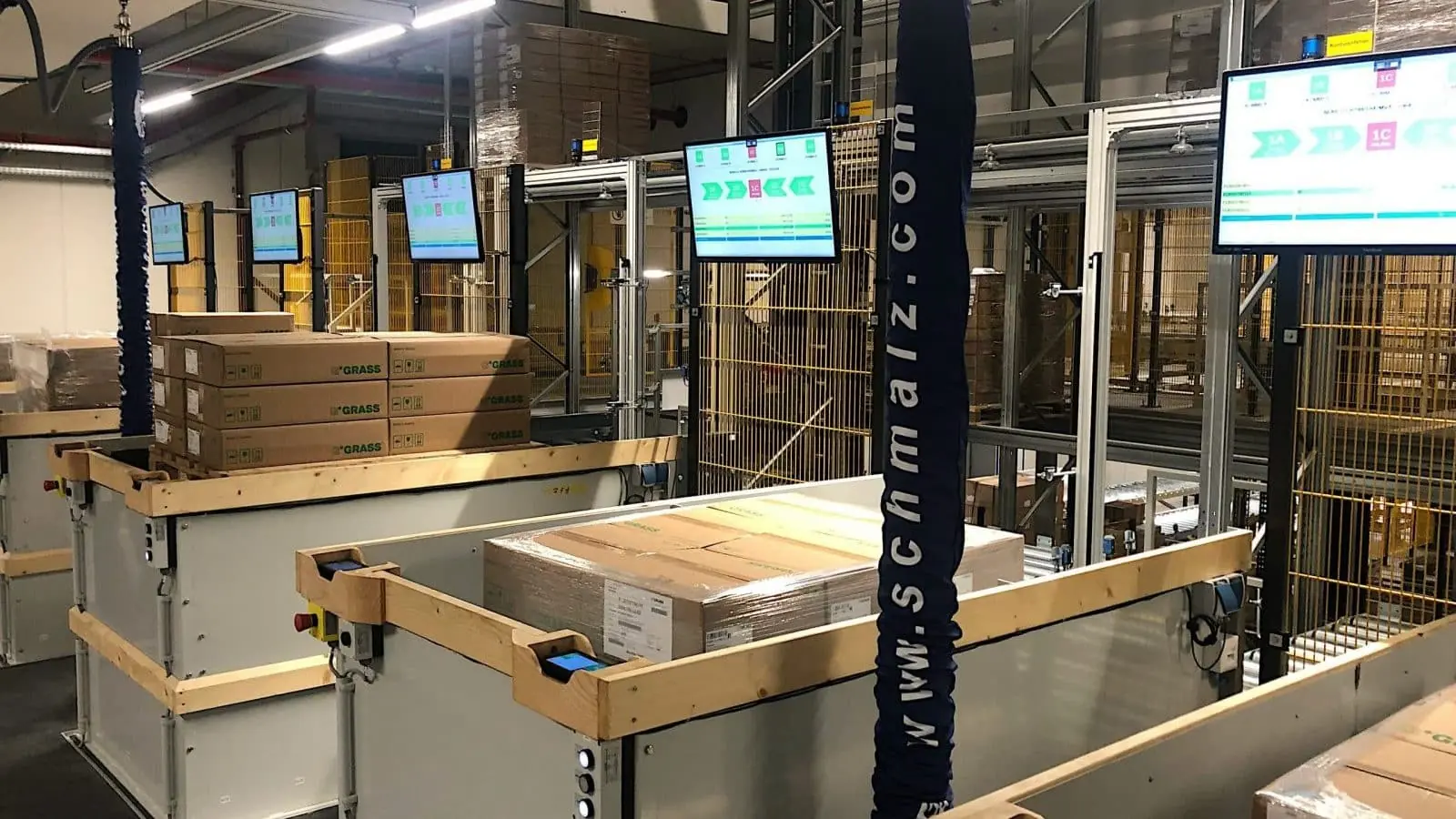
How was the cooperation in terms of response speed and quality?
Direct contact with the project team was mainly via the project manager. Otherwise, we were connected via multimedia, telephone, web-based project management tools and documentation platforms, as well as video conferences, which we used for daily consultation and, of course, direct documentation. Today, this all serves as an easily accessible reference framework for us.
How did the documentation and filing work?
We got to know Jira through TUP. There, all cases are documented, linked to each other and can also be found easily via the search function. Because the project has been running for a long time, it is now particularly important to have access to all this information, also in order to make decisions in the present. Jira and the documentation platform Confluence make it easy to see what was discussed, what was thought about, what was discarded, and what the current status is.
How did the relocation and outbound restructuring go?
My main focus was the relocation during ongoing operations. We previously had a decentralized structure in Vorarlberg through another warehouse at the Feldkirch site, which was completely manual. In addition, there were two logistics service providers in Vorarlberg, one with almost 9,000 pallet spaces and another with about 2,000, internally in Feldkirch we had 15,000 storage spaces. These had to be brought to Hohenems without interruption during peak load times. We had fixed our go-live for July 2020, so we developed our roadmap accordingly with the following questions: “How do we move the inventory back?”, “From when will the orders be dispatched in Hohenems?”, ” When will the equipment be moved?”, ” By when will the employees relocate?”, “At which point will the training courses take place?” We didn’t intend to build up an additional pool of equipment and employees, instead it was all to go hand in hand. The external storage contracts had to be terminated, service providers informed and the transport orders processed. We celebrated the go-live in Hohenems on time in July: All warehouses had been processed, all employees transferred and trained, while the supply chain towards the customer was not only fully maintained, it actually improved.
Were there any particular interesting scenarios?
With something like a relocation, there is always the plan and what actually happens. Especially when it is not clear when which orders are added, whether there are employee absences or the requirements in the project change. But we coordinated daily on the orders, transport capacities and staff availability. When you consider that you’re trying to transfer 15,000 to 20,000 pallets as little as possible, but rather sell them off towards the customer and have the newly produced inventory flow into the new warehouse at the same time, it was a very exciting and challenging task.
Did you use certain tools for this purpose in order to master the complex situation?
We simplified the complexity wherever possible. Communication between the central team members, the external partners and those responsible for operations in Hohenems was important. In our case, the entire planning was Excel-based, where we mapped the entire inventory. We compared this every day and thus knew where things were not going well or where we were even ahead of schedule. We acted very dynamically because the market situation changed every day. With Excel, we were able to develop a standard fairly quickly that worked for us. You wouldn’t believe it, but this good old Microsoft tool does accompany you for a very long time.
What are the special features of the facility from your perspective regarding outgoing goods?.
The customs and delivery note processes. The booking and material flow should ideally be synchronous. In Hohenems, we have the issue that until the loading vessel is sent, the load can still change completely because something is defective or the order changes. On the other hand, we have time pressure. We stow a number of containers every day and cannot always wait until the container is fully loaded before we start customs clearance. That’s why we have introduced customs processes that are already started at the picking stage and are only checked again before shipment. We originally came from an area where the outgoing inventory was organized quite manually. Now we use a sequencer. In the best case, the picked inventory is still stored in the high-bay warehouse. 24 hours before delivery, the departure time, the tour and the loading container are created. At this point, we know the departure time of the truck, which shipments will be placed on the loading area and which customers have ordered or even if it is just one customer with several orders. Ideally, all of this is scheduled 24 hours in advance. At least two hours before the departure time is reached, the pallets come fully automatically from the high-bay warehouse into our two shipping buffers with a capacity of about 460 pallets, where we can pre-buffer the shipping volume of the day correctly sequenced per tour.
How deep does the sequencing go, is the pallet itself also sequenced?
We also specify weight sequencing for the pallets.
How did the collaboration go concerning Corona?
Partially, the travel was limited or not possible. Because of that, we switched quite quickly to digital channels with image and sound. This was very efficient, because we could also go out into the warehouse with the camera to show things directly. When it came to the project phase, Corona didn’t hinder us much.
Where does the road ahead go for you and the project?
My job is to further optimize the facility and identify and implement potential for further automation. We collaborate on an almost weekly basis to further optimize the process with the IT team responsible for the warehouse management system – adapting dialogs, for example, to make day-to-day operations even easier. Otherwise, ensuring future growth is covered is a major issue. We have already taken precautions in terms of construction, but internally the focus for the next few years will be on greater efficiency and further automation.
Are there any points that you already have your eye on?
There is a lot of potential in Hohenems in automatic goods receipt. We already have the capability to unload a truck with 33 spaces in two minutes and store everything in just under 17 minutes. From then on, the load is available for our customer orders. The whole solution can also be used on the loading side in the future. What will play a major role in the future is automation in order picking. After the project phase, some robots were already planned so that heavy picks no longer have to be carried out by humans, and instead picking is done automatically from the source to the target pallet. In the project, however, we opted for the safe manual option, since we had already integrated many automation solutions anyway. These are the most exciting fields. At some point, there will certainly be driverless transport systems on the road, and then in ten or fifteen years there will be many new topics and, above all, a lot of potential.
Where is the journey going for you in the near future?
I have already had a great journey and have seen a lot in the company. Currently, I am responsible for operations in the central distribution center. There my goals are to make the processes more efficient and to cover future growth. I haven’t made any other personal plans at the moment, so the next two or three years are well covered. What comes after that, only time will tell.
Thank you very much for the interview!
Click here for the other interviews.