In der Interview-Reihe sprechen wir mit Mitarbeitern der GRASS-Gruppe über die Zusammenarbeit im Projekt Zentrallager Hohenems. Im dritten Teil der vierteiligen Reihe führt Rene Malojer das Wort, den sein Weg vom Einstieg als Werkstudent bis zu der Position des Leiters des Zentrallagers in Hohenems geführt hat.
Was ist deine Position und dein Verantwortungsbereich bei GRASS?
Mein Name ist Rene Malojer, ich bin seit 2013 bei GRASS. Aktuell bin ich zuständig für das Zentrallager am Standort Hohenems. Gestartet bin ich in der strategischen Logistik im berufsbegleitenden Studium, dann ging mein Weg über die Werkslogistik, Leitung Werkslogistik, Leitung Versandsteuerung und schlussendlich hin zum Leiter des Zentrallagers Hohenems seit Mai 2021.
Du hast dich also durch mehrere Abteilungen und verschiedene Perspektiven bewegt?
Ich komme klassisch aus dem Projektgeschäft, übernahm dann Personalverantwortung im Werk und habe mich auf das Themenfeld Order-to-Cash-Prozesse im Auftragszentrum mit der Fragestellung „Wie kommen die Aufträge rein?“ spezialisiert. Jetzt befasse ich mich mit den operativen Prozessen im Lager: Warenein- und ausgang, Kommissionierung sowie die anfallenden Zollthemen.
Wann und wie bist du zum Projekt Hohenems gestoßen?
Das kommt darauf an, wie man den Projektrahmen absteckt. Begleitet hat es mich bereits nach dem ersten Jahr bei GRASS. 2014 ging es darum die dezentrale Lagerstruktur zu überdenken und die Frage zu beantworten, wo die Reise hingehen soll: Wie sollen wir uns zukünftig aufstellen? Wie verwirklichen wir die Ergebnisse der initialen Make-or-Buy-Analyse? Wie sollen die Warenströme aussehen und wo soll das neue Lager entstehen. Im Prinzip war ich von der frühen konzeptionellen Phase an dabei.
Wie war die Zusammenarbeit mit TUP aus der persönlichen und fachlichen Warte?
Zu Beginn gab es einen Wechsel der Projektmitglieder auf beiden Seiten, was am Anfang das tägliche Projektgeschäft etwas behindert hat. Das hat sich aber rasch auf beiden Seiten geklärt und auch zu einer sehr guten persönlichen Basis geführt. Wir konnten schnell auf Augenhöhe kommunizieren und beide Seiten haben spannende Sparringspartner gewonnen: Auf der einen Seite wir von GRASS, die die Erfahrung aus der Vergangenheit mit an den Tisch gebracht haben und auf der anderen Seite TUP, die vergleichbare Projekte umgesetzt haben und auch am Puls der Zeit waren, was Anforderungen und Umsetzungsmöglichkeiten angeht. Wir hatten also während der Projektphase und auch danach einen sehr guten Partner auf der persönlichen und fachlichen Ebene.
Gabe es eine Situation, in dem das Prozesswissen von GRASS und die Marktperspektive von TUP besonders gut zusammengefunden haben?
Ganz speziell in der Kommissionierung würde ich sagen. Der Bereich ist ein Hybridsystem, in dem die Picks auf dem Bildschirm und auf ‚Smart Devices‘ angezeigt werden. Auch die Quell- und Zielpaletten werden dargestellt und der Mitarbeiter wird zu diesen intuitiv geführt. Hier ist diese Erfahrung von GRASS und die Zukunftsperspektive von TUP ideal zusammengeflossen.
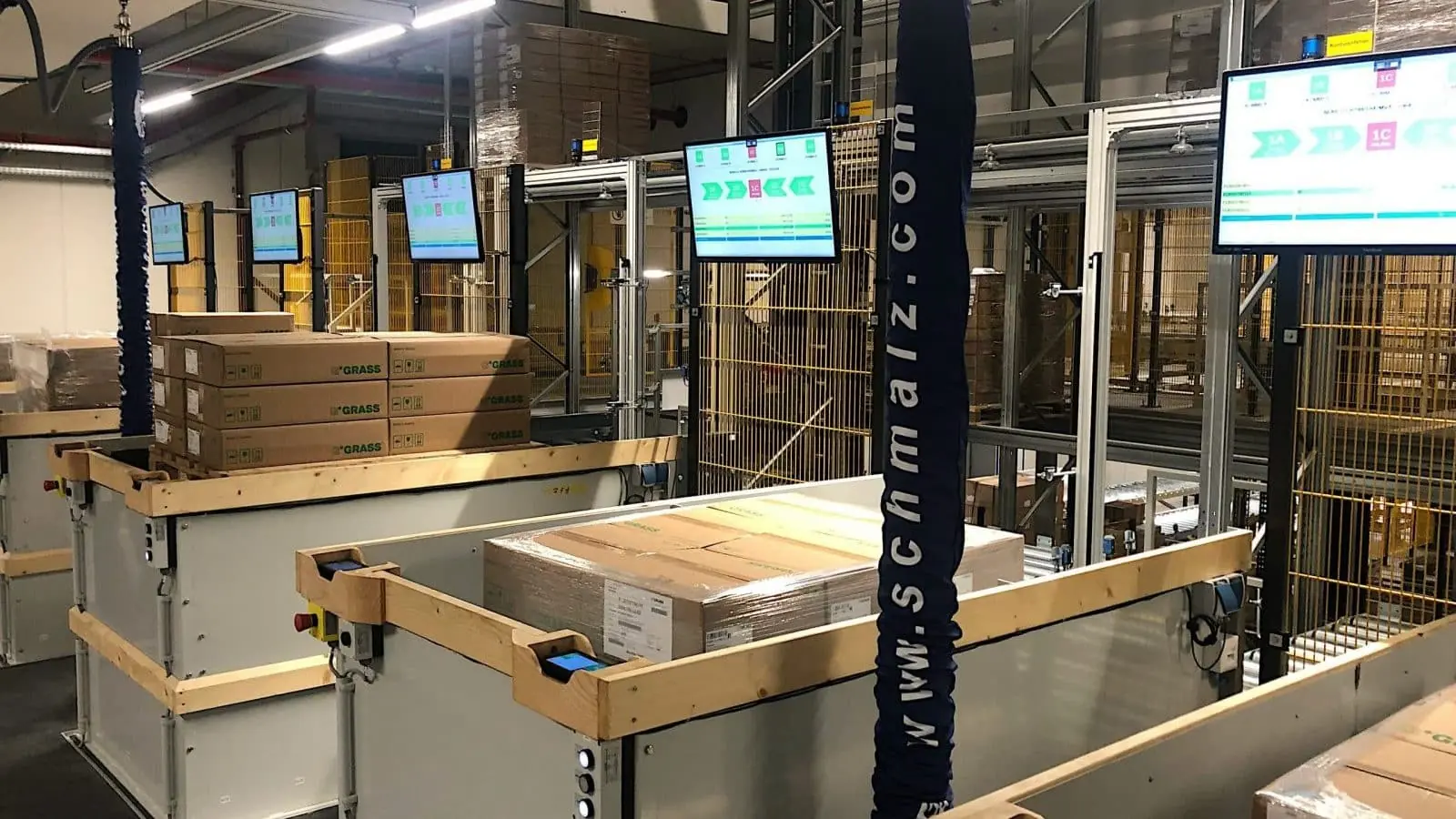
Wie war die Zusammenarbeit im Hinblick auf Reaktionsgeschwindigkeit und Qualität?
Der direkte Kontakt zum Projektteam lief bei uns überwiegend über den Projektleiter. Ansonsten waren wir multimedial verbunden, über Telefon, webbbasierte Projektmanagement-Tools und Dokumentationsplattformen sowie Videokonferenzen, über die wir uns täglich abgesprochen und das Ganze natürlich direkt dokumentiert haben. Das dient uns heute alles als leicht zugängliches Nachschlagewerk.
Wie funktionierte die Dokumentation und Ablage?
Wir haben durch TUP Jira kennengelernt. Dort sind alle Fälle dokumentiert, miteinander verknüpft und über die Suchmaske auch gut zu finden. Dadurch, dass sich das Projekt über einen langen Zeitraum gezogen hat, ist es jetzt besonders wichtig Zugriff auf diese ganzen Informationen zu haben, auch um in der Gegenwart Entscheidungen zu treffen. Durch Jira und die Dokumentationsplattform Confluence ist es leicht nachzuvollziehen was besprochen wurde, was die Denkansätze waren, was verworfen wurde und was der aktuelle Stand ist.
Wie liefen die Verlagerung und die Restrukturierung des Warenausgangs?
Mein Schwerpunkt war die Verlagerung im laufenden Betrieb. Wir hatten zuvor eine dezentrale Struktur in Vorarlberg durch ein weiteres Lager am Standort Feldkirch, das komplett manuell war. Zusätzlich befanden sich zwei Logistikdienstleister in Vorarlberg, einer mit knapp 9.000 Palettenstellplätzen und einer weiteren mit ca 2.000, intern in Feldkirch hatten wir 15.000 Stellplatze. Die galt es während der Vollbelieferung ohne Unterbrechung zeitnah nach Hohenems zu bringen. Unseren Go-Live hatten wir auf den Juli 2020 fixiert, dementsprechend haben wir unseren Fahrplan mit den folgenden Fragestellungen entwickelt: „Wie fahren wir die Ware zurück?“, „Ab wann werden die Aufträge in Hohenems eingetaktet?“, „Ab wann wird das Equipment umgezogen?“, „Ab wann ziehen die Mitarbeiter um?“, „Ab wann finden die Schulungen statt?“ Wir hatten nicht vor einen zusätzlichen Pool an Ausrüstung und Mitarbeiter aufzubauen, sondern das sollte alles Hand in Hand laufen. Die externen Lagerverträge mussten gekündigt, Dienstleistern informiert und die Transportaufträge abgewickelt werden. Wir haben zeitgerecht im Juli den Go-Live in Hohenems gefeiert: Alle Läger waren abgewickelt, alle Mitarbeiter transferiert und geschult, während die Versorgungskette in Richtung Kunde nicht nur vollständig aufrechterhalten wurde, sondern sich sogar positiv entwickelt hat.
Gab es da besondere interessante Szenarien?
Bei sowas wie einer Verlagerung gibt es immer den Plan und das, was tatsächlich passiert. Gerade wenn nicht klar ist, wann welche Aufträge dazukommen, ob es Mitarbeiterausfälle gibt oder sich die Anforderungen im Projekt ändern. Aber wir haben uns täglich zu den Aufträgen, den Transportkapazitäten und der Personalverfügbarkeit abgestimmt. Wenn man bedenkt, dass man da versucht 15.000 bis 20.000 Paletten so wenig wie möglich zu transferieren, sondern eher in Richtung Kunde abverkauft und zeitgleich die neu produzierte Ware ins neue Lager einfließen lässt, war das eine sehr spannende und herausfordernde Aufgabe.
Habt ihr dazu bestimmte Tools eingesetzt, um der komplexen Sachlage Herr zu werden?
Wir haben die Komplexität vereinfacht, wo es nur ging. Wichtig war dabei die Kommunikation zwischen den zentralen Teammitgliedern, den externen Partnern und den operativ Verantwortlichen in Hohenems. Bei uns war die komplette Planung excelbasiert, dort haben wir die gesamten Lager abgebildet. Das haben wir jeden Tag gegenübergestellt und wussten so, wo es nicht gut läuft oder wo wir dem Zeitplan sogar voraus waren. Wir haben sehr dynamisch agiert, da sich die Marktlage jeden Tag verändert hat. Mit Excel konnten wir recht schnell einen Standard entwickeln, der für uns funktioniert hat. Man glaubt es nicht, aber dieses gute alte Microsoft-Tool begleitet einen doch sehr lange.
Was sind die Besonderheiten der Anlage aus deiner Perspektive im Hinblick auf den Warenausgang?
Die Zoll- und Lieferscheinprozesse. Der Buchungs- und Materialfluss soll idealerweise synchron sein. In Hohenems haben wir die Thematik, dass sich bis zum Versenden des Ladegefäßes die Ladung noch komplett verändern kann, weil etwas defekt ist oder sich der Auftrag verändert. Auf der anderen Seite haben wir zeitlichen Druck. Wir stauen täglich etliche Container und können nicht immer abwarten, bis der Container vollständig beladen ist, um dann erst die Verzollung anzugehen. Daher haben wir Zollprozesse eingeführt, die bereits in der Kommissionierung gestartet und nur vor der Versendung nochmal geprüft werden. Wir kommen ursprünglich aus einem Bereich, in dem der Warenausgang recht manuell organisiert war. Jetzt setzen wir einen Sequenzer ein. Die kommissionierte Ware ist im Bestfall noch im Hochregallager eingelagert. 24 Stunden vor der Auslieferung wird der Abfahrtszeitpunkt, die Tour und das Ladegefäß angelegt. Zu diesem Zeitpunkt wissen wir die Abfahrtszeit des LKWs, welche Sendungen auf die Ladefläche kommen und welche Kunden geordert haben oder ob es sogar nur ein Kunde mit mehreren Bestellungen ist. Das alles ist idealerweise 24 Stunden vorher eingetaktet. Spätestens zwei Stunden bevor der Abfahrtszeitpunkt erreicht ist, kommen die Paletten vollautomatisch aus dem Hochregallager in unser zwei Versandpuffer mit ca. 460 Paletten Kapazität, in dem wir das Versandvolumen des Tages korrekt sequenziert pro Tour vorpuffern können.
Wie tief geht die Sequenzierung, ist die Palette selbst auch sequenziert?
Wir geben für die Paletten noch eine Gewichtssequenzierung vor.
Wie lief die Zusammenarbeit im Hinblick auf Corona?
Teilweise war der Reiseverkehr eingeschränkt oder nicht möglich. Da sind wir recht schnell auf digitale Kanäle mit Bild und Ton umgeschwenkt. Was sehr effizient war, da wir mit der Kamera auch ins Lager rausgehen konnten, um Dinge direkt zu zeigen. In der Projektphase hat uns Corona nicht wesentlich behindert.
Wohin geht der weitere Weg für dich und das Projekt
Meine Aufgabe ist die Anlage noch weiter zu optimieren und Potential für weitere Automatisierung zu identifizieren und umzusetzen. Wir arbeiten nahezu wöchentlich daran, um mit dem für das Lagerverwaltungssystem zuständigen IT-Team weiter zu optimieren und beispielsweise Dialoge anzupassen, um das tägliche Doing noch einfacher zu gestalten. Ansonsten ist das Wachstum der Zukunft sicher abzudecken ein großes Thema. Da haben wir schon baulich vorgesorgt, aber intern ist da mehr Effizienz und weitere Automatisierung der Fokus der nächsten Jahre.
Gibt es da Punkte, auf die du bereits jetzt ein Auge geworfen hast.
Es gibt in Hohenems viel Potential im automatischen Wareneingang. Wir haben da jetzt schon die Möglichkeit, dass wir in zwei Minuten einen LKW mit 33 Stellplätzen entladen können und alles in knapp 17 Minuten eingelagert ist. Ab dann ist die Ladung für unsere Kundenaufträge verfügbar. Das Ganze kann zukünftig auch beladeseitig eingesetzt werden. Was in der Zukunft eine wesentliche Rolle spielen wird, ist die Automatisierung in der Kommissionierung. Nach der Projektphase war bereits der eine oder andere Roboter geplant, damit schwere Picks nichts mehr von Menschen durchgeführt werden müssen, sondern dass von der Quell- auf die Zielplatte automatisch kommissioniert wird. Im Projekt haben wir allerdings auf die sichere manuelle Variante gesetzt, da wir ohnehin schon viele Automatisierungslösungen integriert hatten. Das sind die spannendsten Felder. Irgendwann wird es mit Sicherheit auch fahrerlose Transportsysteme im Straßenverkehr geben, dann wird es in zehn oder fünfzehn Jahren viele neue Themen und vor allem viel Potential geben.
Wohin geht die Reise für dich in der nächsten Zeit?
Ich habe schon eine bewegende Reise hinter mir und habe viel im Unternehmen gesehen. Aktuell bin ich im Zentrallager operativ verantwortlich. Da sind meine Ziele die Prozesse effizienter zu gestalten und das zukünftige Wachstum abzudecken. Weitere persönliche Pläne sind gerade keine geschmiedet, die nächsten zwei oder drei Jahre sind damit auch gut abgedeckt. Was danach kommt, wird die Zeit zeigen.
Vielen Dank für das Interview!
Hier geht es zu den weiteren Interviews.