Definition of replenishment in transport and intralogistics
Replenishment is a fundamentally important process in today’s merchandise management. With the best possible integration into the existing warehouse management, it contributes significantly to the efficiency of the material flow. Replenishment is a so-called stock replenishment, which is used to refill warehouses or picking locations in picking zones (for example, from reserve warehouses or reserve locations). Replenishment can be triggered by a pre-emptive strategy, on-demand, or based on a stock-out in the warehouse. To optimise the flow of inventory and existing stock, replenishment is managed through the warehouse management system (WMS).
In intralogistics, replenishment describes a business process that takes place before, during or after picking. This type of inventory replenishment ensures that inventory of goods is maintained within a storage area.
While this type of replenishment is intralogistic in nature, there is also external replenishment, when it comes to ensuring continuous stocks in warehouses of distribution centres or manufacturing companies through transport logistics.
Replenishment – variants and procedures
The supply of goods can be preemptive, on-demand or necessary due to a shortage in the warehouse. The different variants of replenishment can be combined depending on the warehouse planning; also to achieve a balanced system utilisation with maximum delivery readiness.
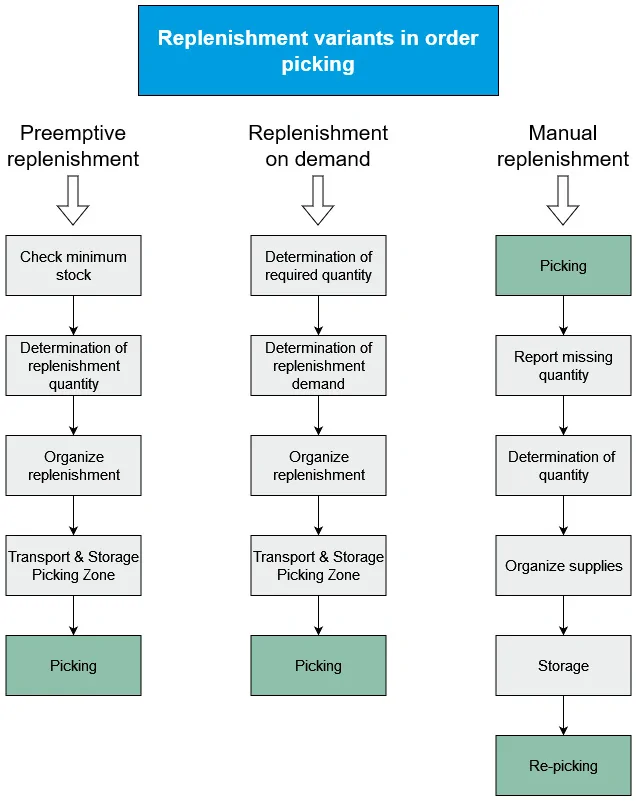
Depending on what triggers the replenishment, we speak of different procedures, which in turn depend on consumption, stock or time. The procedures are as follows and are based on the mentioned triggering criteria:
- Supply procedure (consumption dependency) à Trigger criterion: Consumption
- Reorder point procedure (stock dependency) à Trigger criterion: Reaching the reorder point
- Cycle time procedure (time dependency) à Trigger criterion: Planning time
For each of the three procedures, the following options can be used with regard to the replenishment quantity:
- Minimum replenishment quantity
- Optimal replenishment quantity
- Replenishment quantity to a target stock
Depending on the trigger criteria for replenishment, their combination with the three replenishment options results in 9 different replenishment strategies.
A replenishment strategy should, with minimal effort, ensure a high availability of raw materials, semi-finished parts, materials and inventories in the respective warehouses and access points. Ultimately, the key function of replenishment is to prevent stock levels from falling below a specified minimum level, to avoid stockouts and to ensure a smooth flow of materials; from the outside through transport logistics and from the inside through intralogistics.
The following graphic illustrates a preemptive replenishment with a replenishment quantity to the target stock, as well as a replenishment on demand with the minimum quantity that exactly covers the demand:
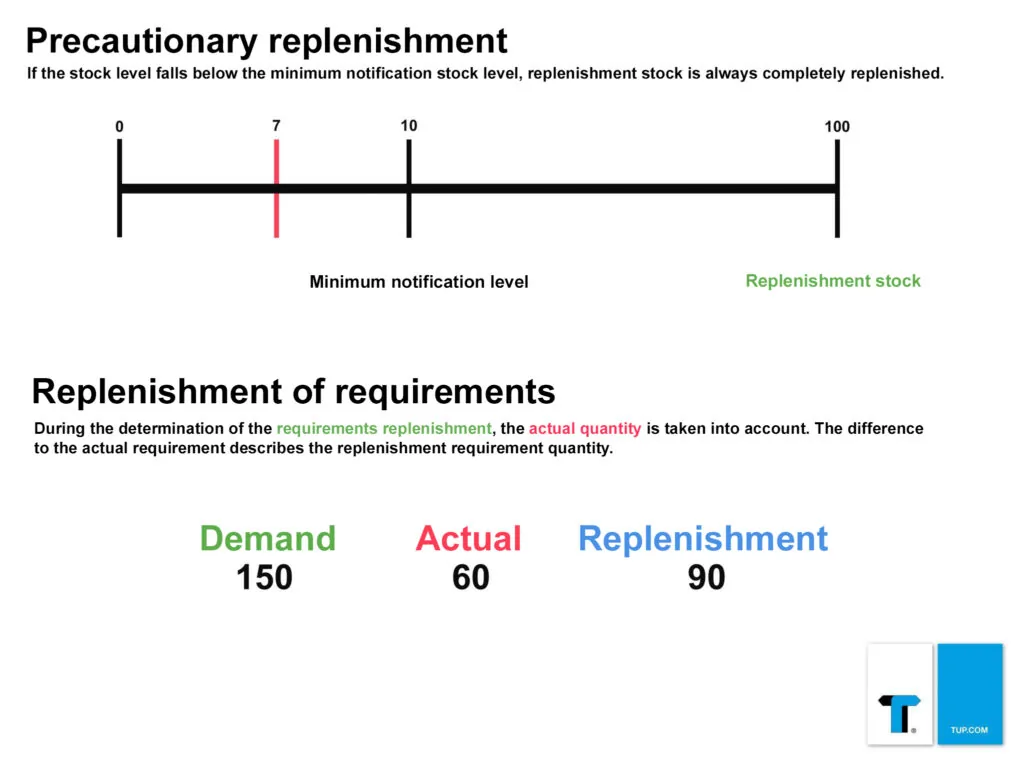
The individual replenishment procedures are described in more detail below:
Replenishment – Staging Area Procedure
Of the three replenishment procedures, the staging area procedure is particularly suitable for replenishing the staging buffer of a point of consumption, for example an assembly line, in a self-regulating manner. Accordingly, the characteristic of this procedure is consumption-based replenishment.
Basic principle of the staging area procedure
In the pre-buffer area, one unit waits to be replenished to the next area. Replenishment to the next area occurs as soon as the contents have been consumed. The storage unit then automatically moves to a staging location.
Two replenishment options
Consumption-based replenishment contains two replenishment options.
- One option involves replenishing the buffer storage location. When a replenishment unit is delivered, the system checks whether there is free storage space in the pre-buffer area for further units. Free buffer storage locations are then filled with units.
- The other option concerns the removal of storage units from the staging location. In this case, the system checks whether the area still contains consumption units. If this is not the case, replenishment is requested.
Advantages and disadvantages of the staging procedure
Compared to the reorder point procedure and the cycle time procedure, the advantage of the staging procedure is that it maintains a self-regulating, minimal stock level and short replenishment time. The disadvantage is the increased replenishment costs that arise if the replenishment quantity is set too low or material consumption increases very quickly.
Replenishment – Reorder point procedure
The reorder point procedure is also known as the order point procedure, the characteristic of which is stock dependency. A reorder point is an inventory quantity at which a process is triggered that results in replenishment or a purchase order. As a sub-area of ordering policy, it is also referred to as a reorder point system, which, from the perspective of warehousing/warehouse management, belongs to consumption-based material planning and consumption-based ordering procedures.
The reorder level ensures stock availability for production and trade and provides a guideline for when replenishment or reordering is necessary. It should be distinguished from the minimum stock level (safety stock), which is intended to prevent production or delivery failures, for example, if a delivery is late or damaged.
Basic principle of the reporting inventory procedure
When a purchase requisition is received, the system checks whether the reporting level will be exceeded by this requirement posting.
The reporting level procedure contains two replenishment options in the event that the reporting level is reached or exceeded.
- Order point-dependent individual planning: When the reorder point is reached, an optimal replenishment quantity is ordered. The replenishment order for each item is independent of the replenishment requirements of other items.
- Order point-dependent collective planning: When the reorder point of an item is reached, a check is made of all items from the same delivery point. This involves checking whether the difference between the current target stock and the actual stock is greater than the minimum replenishment quantity. A collective order is then triggered in the amount of the target stock difference.
Outside of intralogistics, two reporting stock procedures are also distinguished or, above all, two methods are used; on the one hand, the order point system and, on the other hand, the order rhythm system. The former is comparable to the two points above. The latter, on the other hand, is based on a fixed rhythm independently of the actual stock, which is why it is used primarily and almost exclusively when the consumption of goods can be well planned in advance, based on a calculated reorder point.
Compared to the staging method and the cycle time method, the advantage of the reorder point method is the optimal stock level. The disadvantages are the more difficult replenishment coordination and the partially delayed replenishment time. Furthermore, the reorder point must be optimally calculated, for which there are various options, depending on the numerous specifications that can be incorporated.
Replenishment – Cycle time procedure
The cycle time procedure is particularly suitable for replenishment without computer support or when replenishment is to be carried out only after a fixed replenishment cycle. A feature of the cycle time procedure is its time dependency.
A predetermined replenishment cycle is helpful so that the person planning the use of suppliers does not have to be involved in every single order. In addition, the cycle time method allows the supplier to deliver in regular tours. Common forms of replenishment planning are monthly, weekly or even daily replenishment.
There are two replenishment options in the cycle time procedure:
- Cyclical individual replenishment
For each item, a check is made independently at a specific point in time to determine whether the stock level will fall below the reorder level by the following replenishment time. If this is the case, a purchase order is placed for the optimal replenishment quantity.
- Cyclical collective replenishment
For all articles of the same delivery point, a check is made at a certain point in time to see if the target stock difference is greater than the required replenishment quantity. If further articles are required, a collective purchase order is triggered for the relevant delivery point.
On average, the optimal replenishment quantity is delivered half a period too early. Compared to the reorder point procedure, the average stock level is therefore higher when replenishment is planned using the cycle time procedure. The advantage is that it is possible to coordinate replenishments for several items at the same time. The disadvantage is the high space costs and the limited space available per item.
Replenishment planning in intralogistics
A key function that must be closely linked to picking is the classic replenishment from the main warehouse (reserve warehouse) directly to the picking zone. This is also the reason why the warehouse topology already plays an important role during warehouse planning.
A replenishment warehouse can be divided into several separate areas according to the goods groups or the corresponding load carriers (pallet, box, plastic container or other handling aids). With such a separation, several complete logistics units of a good are usually stored in the replenishment area with a large storage capacity, for example, fully loaded pallets. In the picking area, on the other hand, there are primarily partial logistics units. If these run low, corresponding units are replenished from the supply warehouse. The advantage of this is that the number of units in the picking area is kept small, making it easier for employees to access them.
The challenge in supply planning:
- different storage location types (pallets, small parts)
- different warehouse designs: aisle route, flow aisle, one-way street, dead end
- different tools: pallet truck, forklift, person with or without a trolley
Nachschub – Kennzahlen
On the basis of the corresponding warehouse key figures, both the efficiency and the productivity and quality of the replenishment can be assessed. The following key figures are therefore important for the control centre:
- The number of replenishment cycles
- The number of replenishment movements (relocations)
- The number of ‘golden cartons’ (these are cartons containing inventory that can be routed directly from the warehouse to the sorter (packing area) without having to go through the picking process first)
- Start and end of replenishment
- Withdrawal and delivery compartment (source and destination)
To measure the objectives of warehouse supply and replenishment, the key figures for the following work steps play a role:
- route section
- capacity utilisation
- work progress
- shortage
The recipients of the key figures are the logistics manager, the warehouse manager and other employees who work in the warehouse.
Summary
Replenishment is an extremely important process for ensuring production and delivery capacity in retail and industrial companies. Different replenishment variants are used in a warehouse or company: manual replenishment, preemptive replenishment and demand-based replenishment. Depending on which trigger criteria are used for the replenishment, there are three replenishment methods, each of which depends on consumption, stock or time: staging method, reorder point method and cycle time method.
These are combined with three options regarding the replenishment quantity: minimum replenishment quantity, optimal replenishment quantity and replenishment quantity to a target stock.
The purpose of replenishment and the corresponding strategies is to ensure a high availability of materials and inventories in the respective warehouses and access points. At best, minimum stock levels are not undershot, stockouts are avoided, and a smooth material flow is ensured in an efficient and economical manner.
For more information on the context of replenishment, see also picking, POS system, warehouse management and store logistics, ship-to line / direct goods provision, buffer section and zero crossing.