Ensuring that certain temperature conditions are maintained is the be-all and end-all in pharmaceutical logistics. Transport service providers and warehouse operators meet this challenge with close monitoring, digital support and optimized processes in supply chain management.
Given the sensitivity of vaccines and medicines, processes here must function 100 percent and meet the strict requirements of “Good Manufacturing Practice“ and “Good Distribution Practice“, which are often grouped under “GxP”. In most cases, a pair of shoes delivered in a different color or the wrong size in e-commerce results only in a return and chagrin; wrong or improperly stored medications lead to serious consequences in the medical treatment of people.
But what happens when the pharmaceutical industry has to change in a matter of weeks, but it has to keep its very high safety standards? This article provides an overview for decision-makers of what definitely needs to be considered in critical change projects under extreme time pressure.
“Even if such a case should only occur every five years, it must be perfectly covered from a technical point of view in the software.” – Nicolas Walther, project manager at TUP
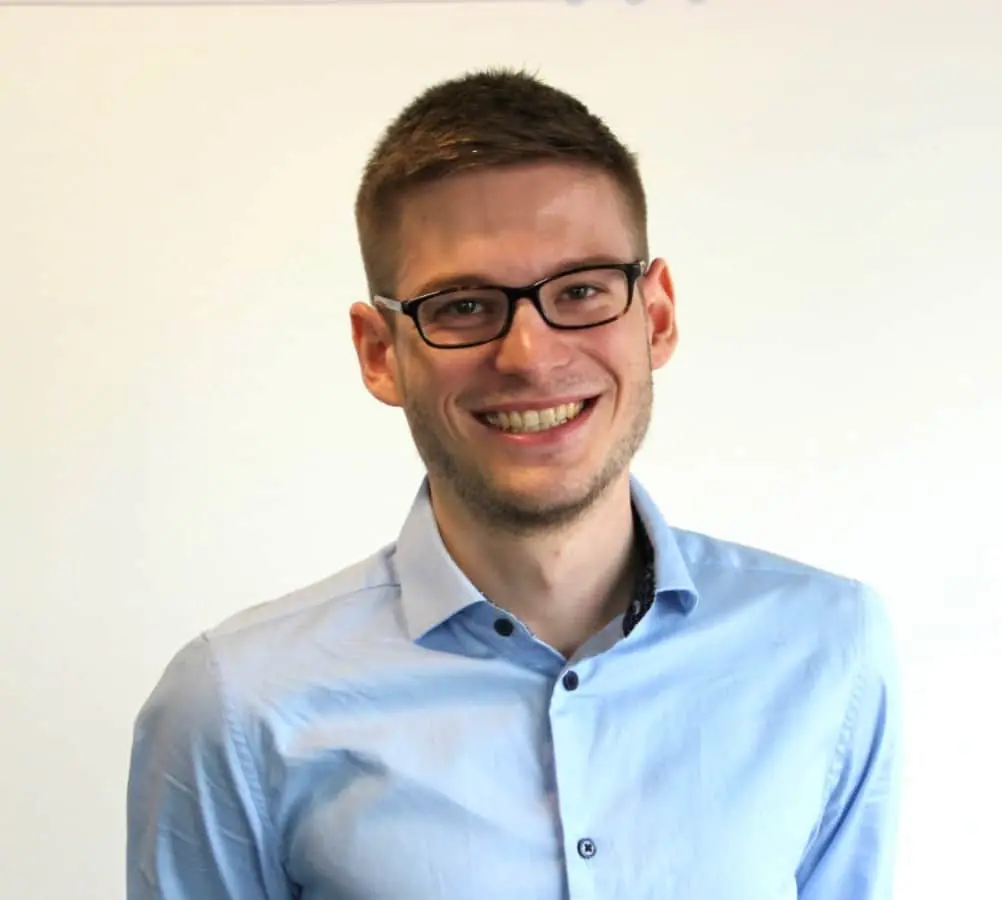
An outlook into the current and possibly somewhat idealized world of pharmaceutical logistics can be found in the Yearbook Logistics 2023 in the article “Impfstoff-Logistik in der Corona-Pandemie – Erfolgsfaktoren für die Integrität der von Pharma-Supply-Chains” by the authors Supriya Kapila, Prof. Dr. Carsten Feldmann and Prof. Dr. Michael Dircksen of Münster University of Applied Sciences: There, the central challenges of the industry are considered at the junctions of the cold chain as well as anti-counterfeiting in the context of vaccine distribution.
In addition to compliance with the legal frameworks for production and distribution, which apply in Europe and worldwide respectively, information transparency and integrity in particular is an important factor for acting quickly, economically and, above all, safely. Vaccines based on lipid nanoparticles, such as the first developments by BioNtech or Moderna at the beginning of the COVID-19 pandemic, often required very low temperatures of -80 to -30 degrees Celsius to maintain their effectiveness.
If, for example, only the temperature of the cold room in the transporter or warehouse is monitored but not the condition of the individual containers, the risk of an undetected temperature overshoot increases. Gaps in documentation due to a lack of real-time monitoring caused by interface problems between individual transport steps or systems also constitute risk sources.
In this graphic, adapted from the English-language technical paper “Tuning value chains for better signals in the post-covid era: Vaccine supply chain concerns,” it can be seen that documentation, temperature monitoring and, above all, staff expertise are the pillars on which IoT technologies can deliver added value to meet the well-known six “r “s of logistics: the right products, in the right quality, the right quantity, at the right place, at the right time, with the right cost.
One of the final steps in this process can be observed by attentive pharmacy visitors when prescription drugs are scanned again before dispensation to verify them. This ensures that the medication is known, not yet dispensed, and not yet expired.
However, with regard to uninterrupted protection of the required temperature range, important steps precede the distribution of medication or the inoculation of patients. This applies not only to transport but also to warehousing.
A closer look at intralogistics in the pharmaceutical industry
The advantage of intralogistics compared to the last mile and other transport paths is that it is a controlled environment. There, hardware and software as well as the processes coupled to them are known and can be changed directly. So when new processes need to be implemented quickly, for example in temperature control, existing best practices provide the framework along which to adapt quickly to the new need.
But what happens when, in addition to the simpler storage of cough syrup or painkillers, an ultra-low temperature (ULT) area needs to be created within a very short time to respond to the effects of a pandemic? Nicolas Walther provides insights into his experience in this type of project and explains what decision-makers must take into account.
The software architecture
The following questions are especially important to ask in this context:
- Are the WMS and other systems designed for modularity from the outset? Can the existing processes and their hardware be enhanced accordingly?
- Is it a monolith? Might a parallel system need to be set up to cover these new requirements?
Die Prozesse
- Eine Anforderungsdefinition wird in den wenigsten Fälle alle Möglichkeiten abdecken, daher muss es Raum und Ressourcen für weitere Ergänzungen geben, die schnell während des Betriebs integriert werden können.
- Soweit möglich, sollten neue Standards in Hard- und Software sofort bedacht und integriert werden. So kann beispielsweise durch die Verwendung einer neuen ZPL-Version (Zebra Programming Language – eine Drucker-Beschreibungssprache) ein künftige Erneuerung für bestehende Prozesse integriert und getestet werden.
- Wenn es schnell gehen soll, müssen alle notwendigen Akteure auch dazu in der Lage sein, umgehend zu (re)agieren: Wenn die letzten fünf Meter Netzwerkkabel fehlen oder die Baugenehmigung länger dauert, steht das Projekt still. Diese möglichen Hindernissen müssen (im Idealfall im Vorfeld) identifiziert und bewertet sowie letztendlich so rasch wie möglich aus dem Weg geräumt werden.
The staff
“These are projects for people who care about details.” – Nicolas Walther
-
- When things need to move quickly and are complex, experience is needed to start with the best first serve. Therefore, the domain experts with the greatest wealth of experience must be available to the project, even if this may mean that other subdivisions temporarily no longer have access to these top professionals.
- Decision paths must be short and always available. The best planning on site often fails if, for example, the corporate headquarters as a approval entity is not closely involved and integrated to decide directly and efficiently.
Data
-
-
- With ever-increasing amounts of data being collected using precise monitoring tools, there is a need for seamless collection and accurate transmission of information to ensure the right conclusions are drawn.
- Frequently, clever approaches to a sub-problem exist as an isolated solution, from which data must then, however, be exported manually and compared on an hourly or daily basis in spreadsheet programs such as Microsoft Excel. Therefore, TUP pursues in such cases the approach of the “data spider”: In the middle of the IT environment one system sits, whose task it is to collect information via interfaces, to catalog them and to pass them on to other systems. This prevents discontinuities in the transfer of information, while ensuring that data is only processed manually when absolutely necessary.
-
Usability
-
-
- When processes become more complex and potentially more and more data is available, the user experience must grow accordingly.
- In particular, user interfaces at mobile data terminals and workstations can provide additional safety and speed through user-friendly design and contextual assistance.
- The critical factor in all steps of the graphic shown above is the availability of highly qualified personnel and the resulting strong ability to act even in exceptional circumstances.
-
If these points are all successfully brought together, then complex processes in the pharmaceutical industry can also be implemented at top speed, while in parallel creating future viability through retrofits or software updates.
An outlook towards the future
“Twenty years ago, pharmaceutical distribution centers were the cutting-edge. They now have to share that rank with other industries. So there is a need for innovation.” – Nicolas Walther
Picking robots, which are in the pipeline or already in use in the e-commerce or automotive sectors, do not (yet) exist in the pharmaceutical sector. This does not necessarily have to do with a lack of willingness to innovate, but rather the logistical requirements of the pharmaceutical industry are very high due to the sensitivity of the products and may still not be satisfactorily met by available solutions.
However, there is still a lot of potential for automation in order picking and incoming goods: in incoming goods, there are already solutions in TUP projects where trucks are unloaded completely automatically, such as in the GRASS warehouse in Hohenems.
For picking robots, the potential lies in preparing appropriate shipments outside of working hours to better accommodate order peaks. As is almost always the case, solutions born of visionary ideas and their concrete technological implementation are mutually dependent. Considering the need to improve the supply of medication and vaccines to patients, every optimization is worthwhile.