The Erwin Müller Group has been the leading mail-order company for catering supplies in Europe for over 25 years. As part of the modernization of its IT infrastructure, the company based in Wertingen, Bavaria, is introducing the ERP system Microsoft Dynamics AX. TUP is responsible for the necessary adaptations to the in-house material flow computer and the Erwin Müller warehouse management system (TUP-ELS) – all on the fly, of course.
After more than 25 years of service, the previous self-developed ERP system (AS/400), based on an IBM i-Series, is literally getting on in years. In order to ensure the further growth of the group of companies with a total of eight subsidiaries, the Erwin Müller Group (EMG) has decided to manage the brand’s VEGA, Hotelwäsche Erwin Müller, JOBELINE as well as Pulsiva, including the more than 40,000 registered articles, company-wide using Microsoft Dynamics AX.
The ERP system: multi-stage commissioning under running wheels
The changeover, which was designed for each client, presented several technical challenges: EMG interacted with various clients and international subsidiaries. Over time, it has become increasingly difficult to reconcile current projects with IT and targeted growth. In addition, the company used the aforementioned ERP system AS/400 during the entire modernization phase. The legacy system was thus kept productive. The AS-400 machine was switched off only after a successful complete replacement and a clearly defined stable running phase.
“The affected clients and catering supplies specialists Pulsiva, VEGA, Hotelwäsche Erwin Müller and JOBELINE appreciated very much that the ongoing operation was not impaired during the multi-stage commissioning”, said Jochen Ried, Deputy Head of Logistics EMG. “The first stage therefore initially included the client Pulsiva, which has already been running on the new host since September 2015. The two other clients VEGA and Hotelwäsche Erwin Müller (incl. JOBELINE) continued to operate via the AS-400 system, as before. However, they were also migrated to the new system landscape in the course of 2016. Hardly anything has changed for the employees in the facility during the conversion. They only experienced facilitating changes such as online invoice printing; the TUP-ELS users did not notice anything of the system changeover”.
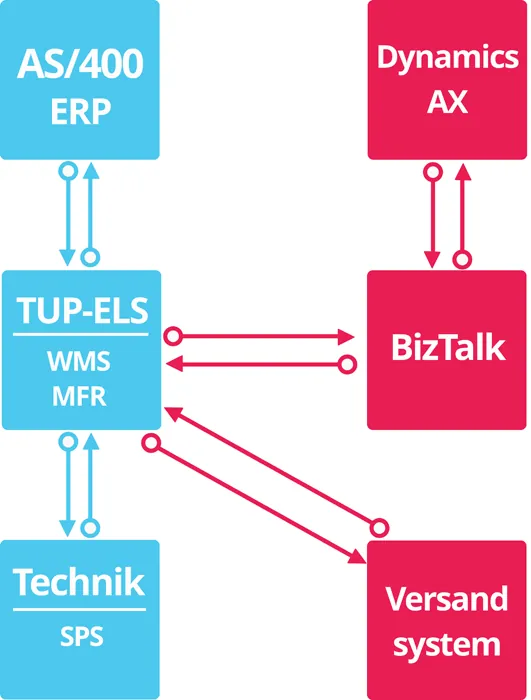
The warehouse management system: special conversation, parallel telegram management
Of course, not everything revolved around the ERP system. “In this respect, we are talking about a system network which, in addition to the ERPs mentioned above, also includes the Enterprise Service Bus BizTalk from Microsoft. Between our TUP-ELS and the AX machine, there is the so-called BizTalk server, which serves as an intermediary layer or translator. All telegrams that we send to the Microsoft system are automatically routed through the BizTalk server and then translated into the AX language and transferred to Microsoft Dynamics AX,” explained Julia Hodecker, industrial engineer and project manager at TUP. The TUP-ELS is therefore programmed on the basis of a special conversation. For certain telegram types, the transmission sequence is automatically specified during operation. If there are no transmission defaults, or if the conversation allows it, the telegrams can also be sent in parallel. The aim of sequencing was to provide the information to the AX system in a process-oriented way.
- EMG target system with Microsoft Dynamics AX: It was planned that the entire logistics would be managed by the new ERP system in 2017. The warehouse management system from TUP (TUP-ELS) handles the material flow, order assignment including invoice printing, and communication with the new shipping system.
Two ERPs and a new carrier system
However, the TUP-ELS received information from two different ERP systems (sequential TUP telegram solution with AS/400 and the known WebServices with the AX system – see above conversation). The orders were subsequently assigned to the so-called commissions of the respective picking types (goods to man, manual sorter picking or bulky parts processing). A pick could extend over several picking types, which in turn were divided into several picking zones. An order could therefore be processed in several picking zones in parallel.
Technically speaking, however, invoice printing in particular is a journey through time. The AS-400 machine still worked with offline-printed invoice stacks, while the AX machine had modern online invoice printing at the packing station. One reason why the sorting modules were equipped differently. Also worth mentioning is the introduction of the carrier system (previously processed via AS/400). Freight costs and shipping type determination were already active at client Pulsiva through the carrier solution from MHP and integrated into the new system landscape. VEGA and Hotelwäsche would follow in the course of the entire AX conversion.
“We were able to handle the first changeover for the client Pulsiva without any major problems and we want to continue this smooth approach with the clients that will follow. The results achieved so far show that EMG has been able to work together with the software manufactory TUP, EMG has backed the right horse,” Julia Hodecker proudly concludes. In the course of the year, a modern customs system (for non-EU clients) was linked to the new ERP system. The entire modernization was completed in 2017.
Our IT-Lösungen at a glance.
Image source: Erwin Müller Group