TUP implemented two large-scale projects for the bicycle manufacturer Canyon. In a short time, a new production site with optimized intralogistics was created, laying the foundation for modern manufacturing and the associated growth potential. As a follow-up project, a cross-site symbiosis of production and warehouse logistics was realized by TUP thanks to individual software solutions, consulting and planning. The result is a scalable overall concept individually tailored to the business processes of the company, which enables the online vendor to ideally exploit the opportunities of the rapidly growing market by consolidating and increasing production capacities by means of digitally controlled line production.
The fact that online retail has developed into a strong economic sector has become clear to everyone at the latest since its sustained boom during the Corona crisis. According to current figures from the German E-Commerce and Mail Order Association (Bundesverband E-Commerce und Versandhandel e.V.), e-commerce in Germany contributes around 100 billion euros/year to the gross domestic product which places it just behind the automotive industry.
For Canyon, a globally popular manufacturer of mountain bikes and road bikes, this is not surprising. The company has relied on online retailing since its founding and is well aware of the advantages: direct interaction increases customer commitment and satisfaction, and bypassing third-party suppliers enables attractive prices.
Another important pillar for sustainable success in e-commerce is scalable, transparent and customized solutions that support manufacturing and logistics processes. This is the only way to respond to the increasingly frequent and intense ordering peaks, which have only been exacerbated by the pandemic. A development that has led to waiting times of up to 500 days for bicycle components in 2022.
A brief overview
TUP implemented two essential projects for the bicycle manufacturer Canyon. First, a new production site with optimized intralogistics was built in a short time, creating the basis for modern manufacturing and further growth potential. As a follow-up project, a cross-site symbiosis of production and warehouse logistics was realized by TUP. The result is a scalable overall concept individually tailored to Canyon’s business processes.
It enables the online vendor to take advantage of the opportunities of the rapidly growing market by consolidating and increasing production capacities through digitally controlled line production.
The starting points of the projects
Faced with steadily growing demand, a solution had to be found to optimize Canyon’s current logistics situation, as existing capacity was fully utilized and spread across different warehouse locations. In order to cope with the increasing number of orders, the company planned to build a new site. Production and intralogistics were to be merged in order to make assembly processes more effective and inventory management and the associated logistics more transparent.
However, this unique challenge could not be met by a standard solution. Therefore, TUP was commissioned to develop a solution specifically adapted to the needs and requirements, to accompany the implementation as general planner for logistics and to optimally support the processes through software. The intralogistics experts from Stutensee near Karlsruhe therefore accompanied the project from conception to implementation, creating more efficient process flows within a short planning and implementation period.
In a second follow-up project with a narrow duration of only three months, TUP was commissioned with the development of a further location. Thus, the software already developed in the first project was operationally extended to another warehouse. TUP tested and implemented this within a very short time, as the software modules could be made instance-capable without version conflicts or incompatibilities. This was possible because TUP constantly accompanied the evolution of Canyon’s processes and introduced a new multi-site solution related to future internationalization as well. As a result, cross-system integration of additional warehouses will be possible without any problems in the future.
How was the first project run and which solutions were used for the warehouse with integrated smart assembly?
At the new Canyon production and product warehouse near Koblenz, production lines and intralogistics were to be made more efficient in order to cope with the increasing demand in e-commerce.
“TUP was the right partner to optimize and automate our logistics processes. In addition, it was important for us to have a partner who would provide us with holistic support in logistics planning, the warehouse management system and warehouse technology as a general planner – all from a single source” – Canyon project manager André Koch
.
The requirements for TUP were, on the one hand, the digitalization of documentation from goods receipt to goods issue, as well as easier access to all data via mobile devices. In addition, digital, two-stage picking was to be introduced and assembly was to be implemented as dynamically controlled line production.
This results in transparent inventories and processes for all employees, as the flow of assembly and goods can now also be displayed and controlled in real-time. This enables Canyon to react quickly and flexibly to the daily order situation.
What were the specifics and requirements during the first project?
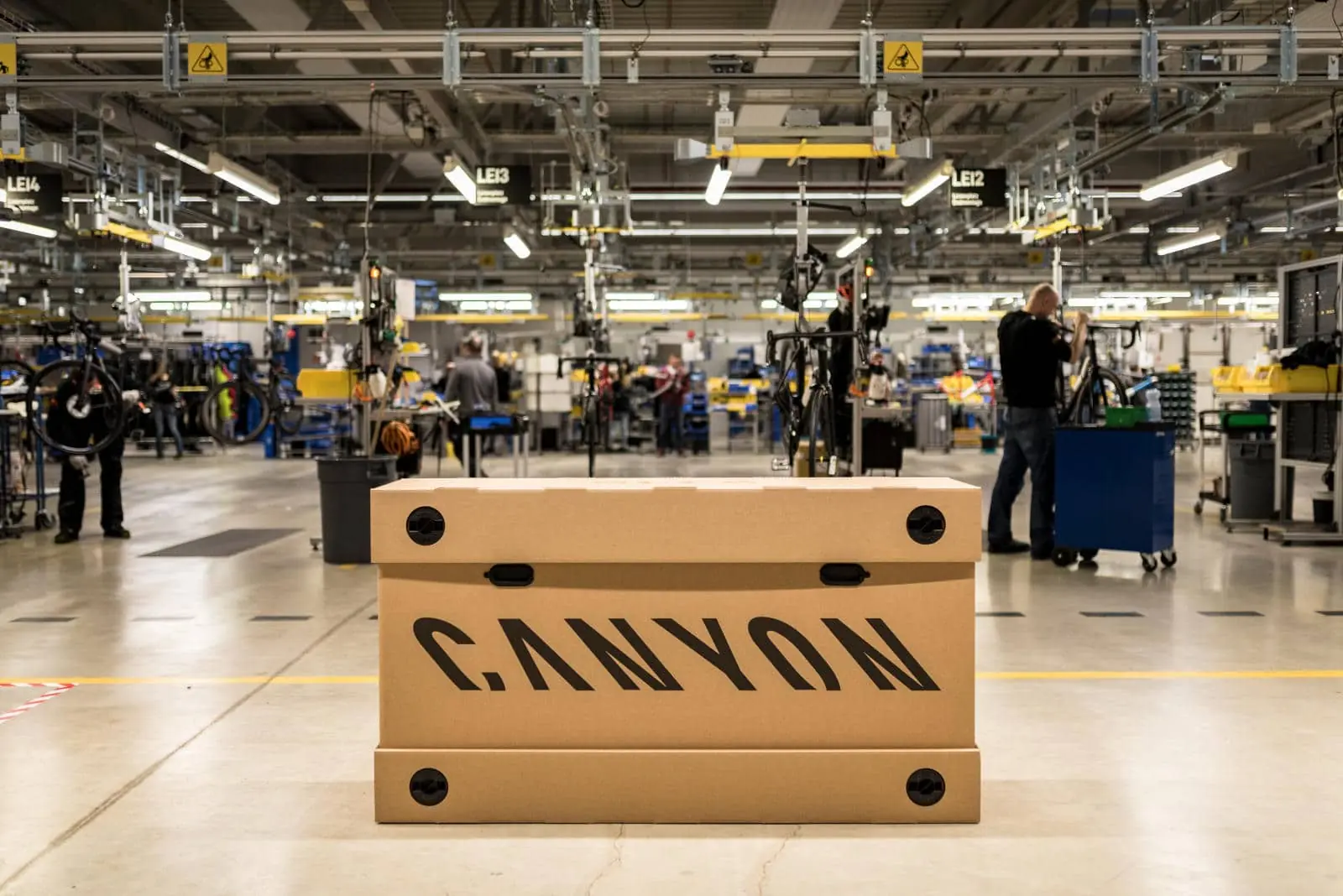
Since TUP provided complete support for the new Canyon Factory building, the company was always able to react quickly to adaptations and implement them individually together with Canyon. Connecting a warehouse management system (WMS) to the assembly line within a brief period of time and completing the entire process from the requirement document to the implementation was a major challenge. TUP was able to complete the project on time and within budget. Canyon’s set goals and expectations were thus met in full.
Furthermore, TUP developed a special modular software for Canyon, called TUP.SML (Smart Mobile Logistics), which enables the use of Android-based end devices but also commercially available smartphones for mobile data collection in the warehouse as well as connecting headsets and ring scanners. These solutions offer Canyon the free choice of handheld devices, a problem-free addition of additional dialogs to the system and enable an uninterrupted production chain. In the event of an unforeseen failure of one device, the work can be continued in the same place with another terminal device thanks to the TUP software.
When the devices equipped with the software are in operation, all data as well as work steps are recorded throughout the entire process chain and transferred to the TUP.WMS warehouse management system developed by TUP. Here, transfer to downstream systems, such as the Enterprise Resource Planning (ERP) system or Manufacturing Execution System (MES) is also possible.
Due to its adaptability, TUP.WMS enables “just-in-sequence” assembly orientation that is dynamic and aligned with the order situation. For this purpose, so-called master and slave tours have been developed to control and efficiently supply the production chains. For example, master rounds consolidate information to bicycle frames. Depending on the position in the production chain, the slave rounds then supply suitable add-on parts for the respective frame. In the process, individual items can also be broken down into components suitable for assembly if they need to be installed at different points in the production line.
TUP.WMS takes over the management of the load carriers, known as carts, which are required as conveyors for order picking, the assembly buffer and delivery. It ensures that sufficient transport capacities are always available.
Furthermore, the TUP modules support the control of materials handling technology between four picking levels (TUP.MFC – material flow controller). A connection layer between TUP solutions, MES and the ERP system enables the efficient integration of further TUP modules or third-party software to control the material flow via a standardized message protocol.
This first individual compilation of TUP solutions, was combined as a functional package “Canyon Logistic System” (CLS), in order to be able to provide the assembly option for further locations if required, which was to be done in the second project step.
What was the second course of the project and which solutions were used for the individual software requirements for each Canyon warehouse?
In a second follow-up project, TUP was commissioned to provide a central networking capability for all Canyon warehouses and specifically for managing the manufacturing plant via a central control center. This creates a high degree of flexibility and short response times in both manufacturing and delivery. TUP Implementation Manager Wolfgang Gilbert recalls, “Without a doubt, the challenge of this project was implementing the software in a period of only three months. The team performed phenomenally and we were able to meet this schedule because we were able to build on the foundations of our software package in the production warehouse near Koblenz.”
What were the specifics and requirements during the second project?
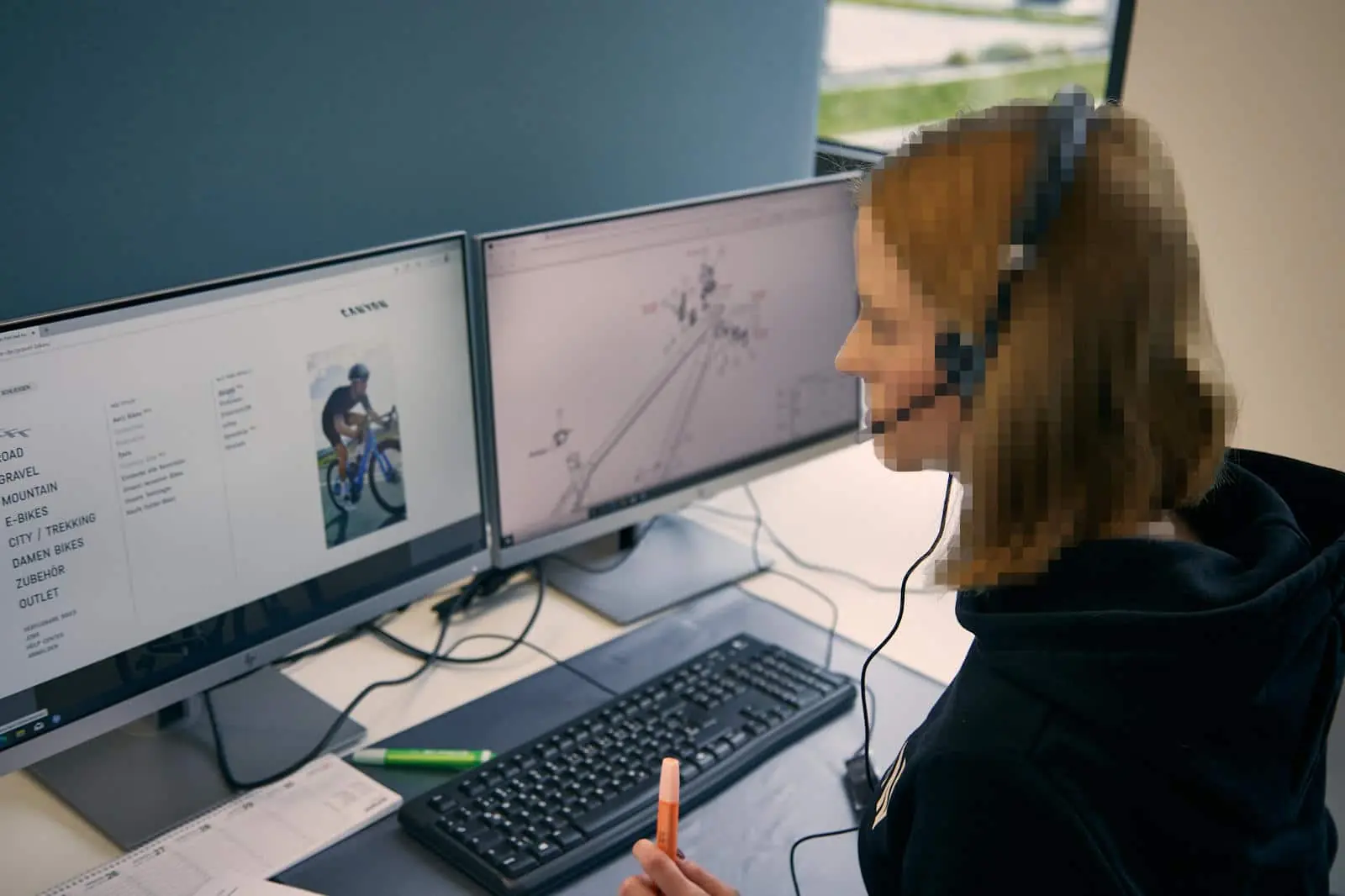
The CLS software was to support an additional warehouse in the next step. For this purpose, another module was developed, which provides the CLS software for one and future additional locations (CLS.GLOBAL). This ensures transparency and further simple, individual adaptation to the requirements of the individual sites.
Since the TUP solutions are mutually compatible, only one new software layer had to be added. Due to TUP’s development approach, this was possible without restricting the functionality of the previously existing software. As a result, Canyon can now access the CLS.GLOBAL global control layer. “There is only one interface, no matter how many decentralized sites are involved, each with their own individual topology,” Gilbert adds. Through custom development, the bicycle manufacturer now has the tools it needs to expand the resilience and scalability of its business model over the long term.
The software provides communication capabilities between higher-level systems, such as CEP service provider systems, and lower-level systems, such as each warehouse’s individual CLS. The software supports every common technology for data and information exchange. The networking enables central monitoring of the TUP.WMS of all warehouses and thus creates a multi-warehouse capability. This means that additional warehouses can be connected at any time, which then benefit in the same way from the ever further evolving features.
The outlook
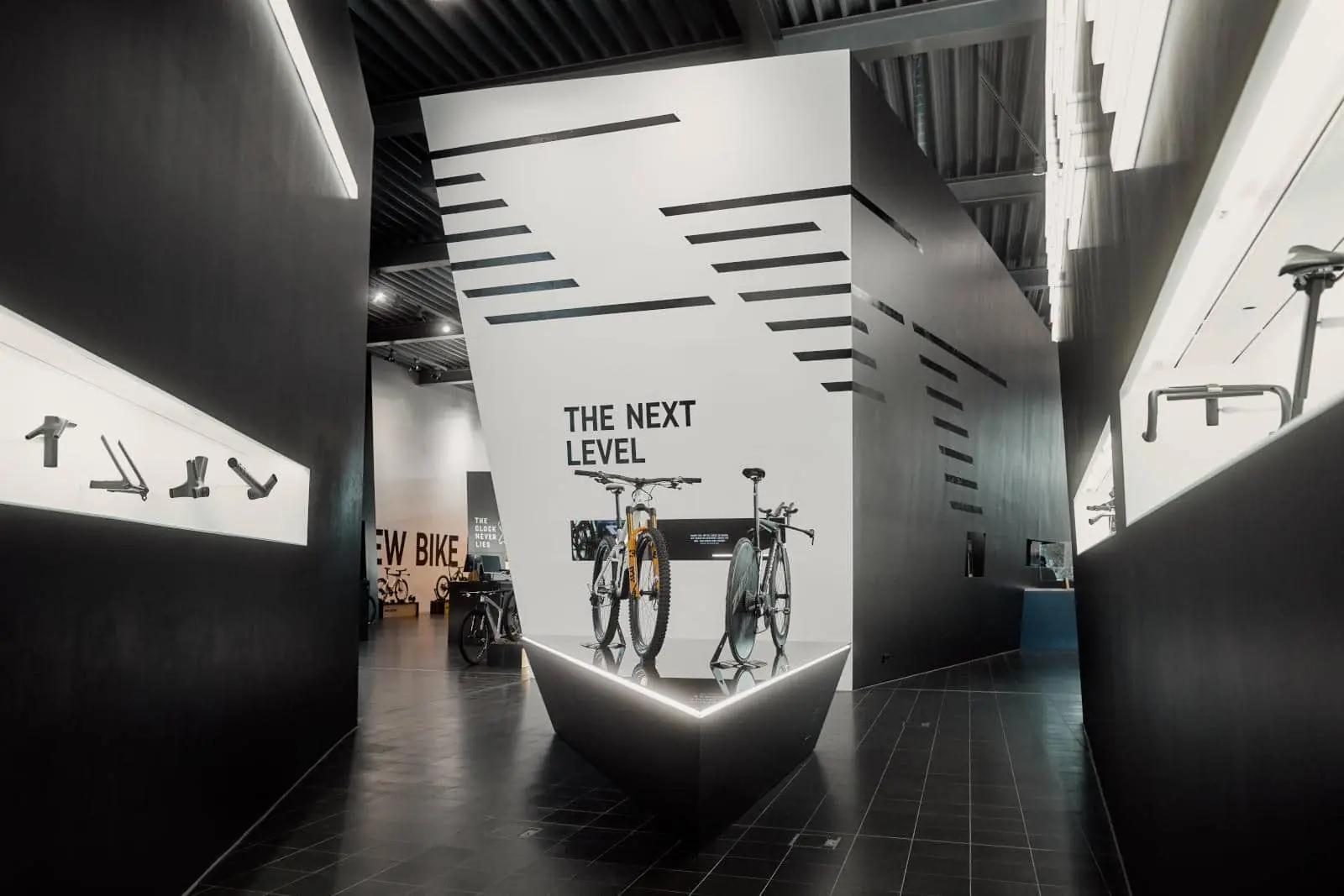
With the software package, Canyon can also expand assembly capacities to other warehouses in the future as needed. The fast and effective adaptations enable the company to continue to satisfy the uninterrupted growth as well as all the requirements of e-commerce and thus to continue to ship bicycles all over the world in the accustomed quality.
This enables TUP, as an IT service provider, to provide Canyon with the best possible support in the face of future challenges in the fast-paced e-commerce market.
This report originally appeared in the 05/2022 issue of the trade journal materialfluss and is available here as a PDF download (German) in an abridged version.