In this series of interviews, we talk to employees of E. Breuninger GmbH & Co. about the joint project for the multi-channel warehouse in Sachsenheim. In the second part of the interview series, we talk to Thorben Pleister, team leader in goods receipt, who gives an insight into the previous situation and the integration of his department’s requirements.
What is your position in the company and what tasks does it involve?
I am the team leader in goods receipt and therefore the disciplinary and technical manager for the area. This includes achieving key figures, process improvements, implementing sub-projects, employee management and personnel planning.
How and when did you join the project and where did you previously work?
I was previously at the former location in Leinfelden. I joined the WDZ project around 2018. There were the first test environments and the open questions were: “What should the structure be like?”, “Are there any technical wishes we still have?” and “What should the systemic processes be like?”
Because we mostly deal with planners or software specialists, your expectations of the collaboration from an operational perspective are very interesting.
The basic attitude towards all partners, including TUP, was to work together in a solution-oriented and partnership-based manner. A solution-oriented approach is particularly important in our dynamic environment.
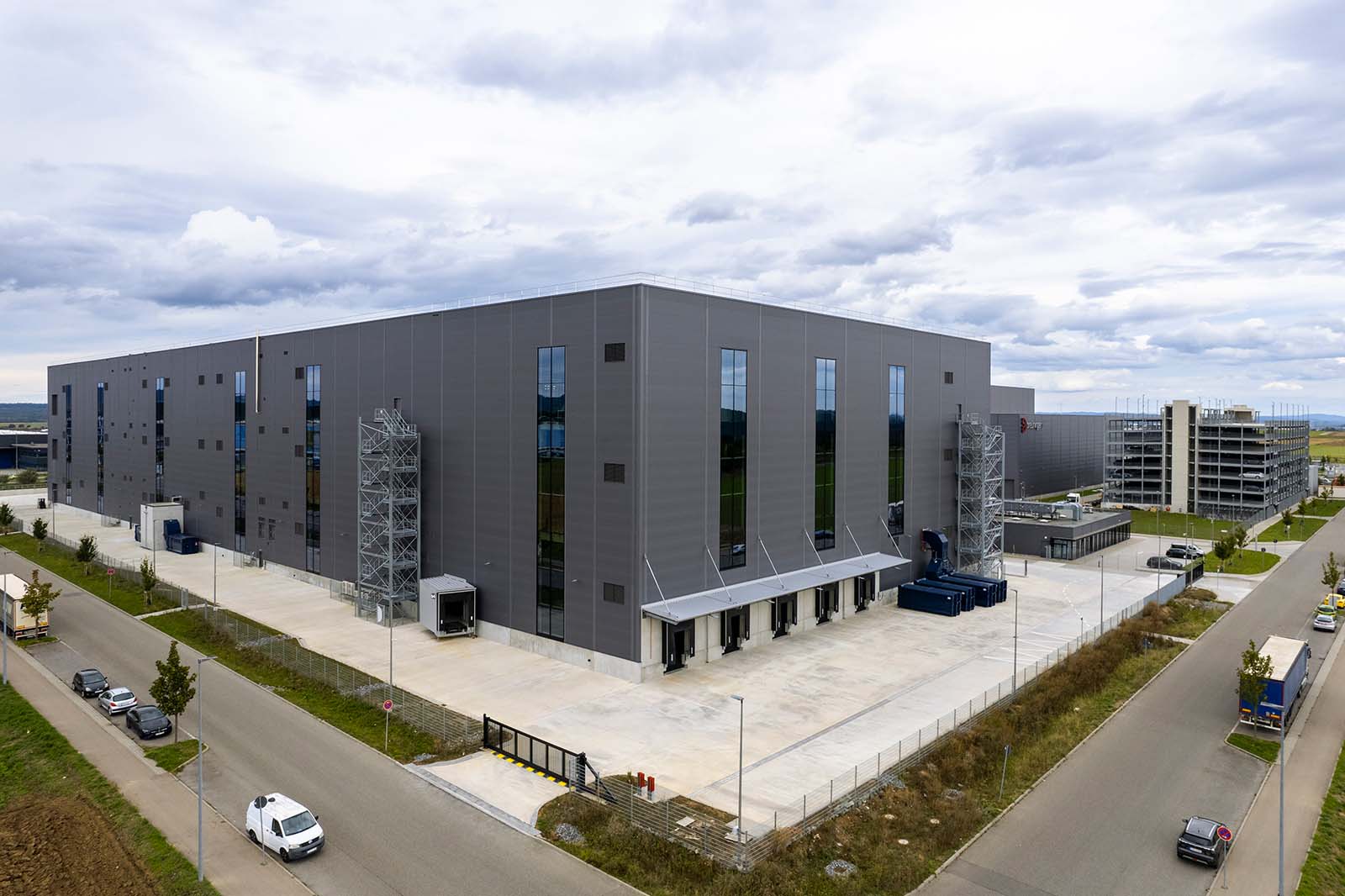
Has this expectation also been fulfilled in the cooperation on a professional and personal level?
Yes, that was definitely the case in the points of contact I had with TUP. Especially during the go-live phase, we were always kept up to date on how things were progressing and which problems were being solved. I found it very positive that I was always kept informed and that issues were prioritized accordingly.
How would you rate the availability, the speed of response and also the quality of the collaboration?
In general, I never had the feeling that anything was stagnating or that things were being ignored or downplayed. Any issues or problems we had were taken up, considered neutrally, dealt with and, if it was really critical, prioritized accordingly. We also always received feedback within a suitable timeframe.
How was the transition from the old logistics world to the new one?
We had a lot of manual processes that we had to solve with significantly more staff. The only way to handle a large volume there was with more people. Here at the new site, technology has made a lot of things much easier for us.
Is there a particular solution that stands out for you?
For me, comparing the old shipping system with the new one was a big talking point. We already had some standardization of the workstations at the old location. But for me it was simply great to see how we have optimized the routes here at the WDZ, that everything is standardized and digitally supported, that training is now easier and that a lot of thought has been given to throughput and productivity. So the move here was the highlight for me. I remember very well the first time I came into the new dispatch hall with the employees from the old locations and was briefly stunned into silence because we immediately realized what we could now achieve.
How did you perceive the support during the various phases?
I can say that it made no difference to me whether we were still in the go-live, hyper-care or after-care phase. The response times, the support and the feeling that everything was being handled promptly were always very good.
Thank you very much for the interview and for your time.
Back to the interview overview
To the Breuninger success story