As a standardized communication interface, VDA 5050 enables the exchange of status and order data between automated guided vehicles (AGVs), automated guided vehicles (AGVs) and a central control system. Before we go into more detail about VDA 5050, however, it’s worth clarifying one question first:
What is the purpose of VDA 5050?
AGVs and FTFs have been used in the automotive industry for decades. Thus, automated transports are commonplace within the industry, but many people are nevertheless not aware of the problems and imponderables that the respective production facilities had to deal with or still have to deal with.
As a rule, each AGV or AGV manufacturer has designed its vehicles and systems in such a way that they can only communicate in the best possible way with their own master control or fleet management software. But in order to use the most suitable AGVs in terms of hardware, a company has to purchase and operate vehicles and systems of different brands. In practice, this then leads to the following negative scenarios:
It becomes difficult to manage the different AGVs when their paths cross.
In order to avoid path crossings and assign separate paths to each AGV, more space must be used.
A separate installation must be performed for each AGV from a respective manufacturer, which makes commissioning complex and costly.
The tendency to therefore only use AGVs/FTFs from a single manufacturer is always present; which can lead to compromises in performance as well as permanent dependency due to the limited product range.
These are serious challenges for companies using AGVs. Heterogeneous AGVs cannot therefore easily exchange (communicate) data with each other quickly or in real time – solving these (communication) problems is the concern of VDA 5050, which meets the desire of many warehouse operators and industrial companies to be able to use driverless systems of different makes with each other in a meaningful way.
What is supposed to get better through VDA 5050?
Mehr Kontext und technische Details (wie beispielsweise das Pull-Prinzip) der Kommunikationsschnittstelle sind im entsprechenden Artikel auf Logistik KNOWHOW erklärt; im Folgenden beschreiben wir kurz, was die VDA 5050 beinhaltet und welche Auswirkungen es hat, auf diesen Standard umzustellen. Denn Standardisierung bedeutet auch, dass nicht alle Hersteller von FTS/FTF ein Interesse daran haben; schließlich verlieren sie dadurch ein gewisses Maß an Exklusivität (Abhängigkeiten) und befürchten eine Austauschbarkeit ihrer Komponenten.
More context and technical details (such as the pull principle) of the communication interface are explained in the corresponding article on Logistik KNOWHOW; in the following, we briefly describe what VDA 5050 entails and the implications of switching to this standard. Because standardization also means that not all AGV/FTF manufacturers have an interest in it; after all, they lose a certain degree of exclusivity (dependencies) as a result and fear interchangeability of their components.
VDA 5050 is intended to enable optimal use of AGVs and AGFs – regardless of the individual makes. This significantly reduces complexity and integration effort. If the infrastructure for VDA 5050 exists, other AGVs and AGVs from other manufacturers can be integrated without any problems, which also applies to the connection of, for example, visualization tools or a replacement of the control system.
This infrastructure includes:
- A message broker (in the case of VDA 5050 the MQTT broker)
- EAP/warehouse management system
- Guidance control system
- Automated guided vehicles
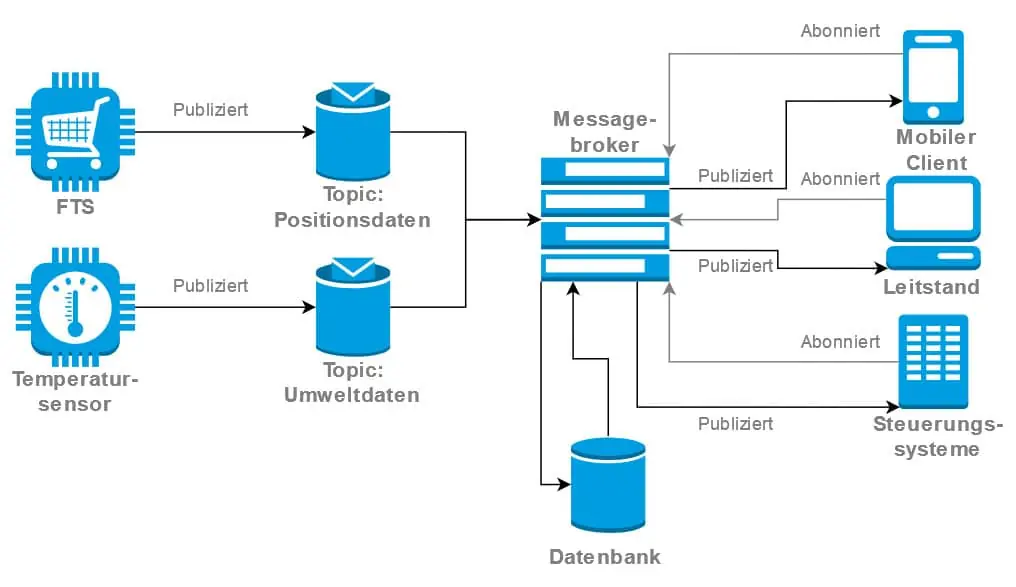
VDA 5050 (current status: version 2.0 from January 2022) is a “work in progress” and is being continuously developed. Over the next two to five years, the standard will most likely become more comprehensive and complete.
The core of the interface definition
VDA 5050 serves to optimize the flow of materials by enabling the communication of the various AGVs/FTFs used through standardization, as well as their simple integration into the existing conveyor landscape.
Driverless transport vehicles can already be connected universally even without standardization. In contrast to other control systems, the operation of harmoniously acting mixed fleets can already be implemented by TUP.
But due to the increased time required and the resulting costs, such multiple connections are hardly ever commissioned at present. Therein lies the charm of the specification, should it find wide application: A standardized interface would speed up integration considerably. A common communication interface would increase the demand for flexible full integration of mixed fleets and it would be an economically viable alternative for more companies to consider. AGVs would thus become more widespread in the warehouse beyond their origins in automotive production than is still the case today.
Smart control of the material flow is always holistic
For an integrated concept like an automated guided vehicle system, software plays just as central a role as hardware. The interaction of the software with all adjacent systems must be stable, reliable and, above all, performant, even if many other vehicles and actors have to be taken into account. Only in this way can the performance potential of AGVs be fully realized. At the same time, it must be kept in mind how the use of this technology affects the given processes and IT structures. The respective AGV must always respond to the given developments without disrupting other processes. Once the synchronized use of different AGVs has been ensured, the first major hurdle has been overcome. The focus then shifts to the performance of the master control system used, which ensures a holistic material flow.
TUP's Material flow control
Unsere individuell und passgenau auf die Anforderungen der Kunden abgestimmte Materialflusssteuerung TUP.MFC orchestriert die gesamte zur Verfügung stehende Lagertechnik und optimiert Lageraufgaben. Sie zeichnet sich in besonderem Maße durch ihre schnelle dynamische Routenplanung aus. Unter Berücksichtigung von Zeitfenstern an Knotenpunkten sowie der Positionen der anderen Transportteilnehmer weist TUP.MFC den optimalen Weg durch die kundenspezifische Förderlandschaft. Auf sich verändernde Gegebenheiten in der Förderlandschaft reagiert sie in Echtzeit. Dazu analysiert und überwacht die Software permanent alle Betriebszustände und verhindert auf diesem Wege Systemunterbrechungen. Die Software erlaubt es zudem, neben FTS auch manuelle Fahrzeuge unmittelbar in den koordinierten Materialfluss einzubinden. Erfahren Sie dazu mehr in einem Fachbeitrag des Magazins DHF Intralogistik.
Our TUP.MFC material flow control system, which is individually and precisely tailored to customer requirements, orchestrates the entire available warehouse technology and optimizes warehouse tasks. It is characterized in particular by its fast dynamic route planning. Taking into account time windows at nodes as well as the positions of other transport participants, TUP.MFC shows the optimal route through the customer-specific conveyor landscape. It reacts to changing conditions in the conveyor landscape in real time. To this end, the software permanently analyzes and monitors all operating states, thus preventing system interruptions. The software also allows manual vehicles to be directly integrated into the coordinated material flow in addition to AGVs. Learn more about this in a technical article in the magazine DHF Intralogistik (german language).
Our perspective on VDA 5050
The central challenge in the integration of self-driving systems results from the different requirements and manufacturers. Often, individual usage scenarios can only be mapped by combining models from different makes. Since not all suppliers have an interest in coordinating their solutions with each other, this leads to the issue of VDA 5050 via the more difficult exchange of data. In order to fundamentally enable the control of a mixed fleet, a central control system and an interface that handles the communication between hardware and software are indispensable.
For TUP solutions, a communication standard would not be technically necessary: Driverless transport vehicles can be universally connected to the TUP.MFC control system even without VDA 5050. However, an interface standardized via the VDA 5050 specification offers enormous advantages in terms of integration speed as well as general future-proofing.
To our other blog articles
Back to the start page
To our software solutions