One of Europe’s most important pharmaceutical warehouses is in operation at the Karlsruhe, Germany, site. Human and veterinary medicines from over 50 production sites worldwide are brought together here and stored in a warehouse with a capacity of 20 million pharmaceutical packages. Every day, around 100,000 of these products, some of which are sensitive, sometimes dangerous, and often vital for patients, are delivered to the German-speaking market as required. As part of Germany’s critical infrastructure (KRITIS), maximum reliability is essential.
Success factor: Long-standing partnership
The warehouse operator’s collaboration with TUP at the site is characterized by exceptionally long-standing stability – almost unique in the IT sector: TUP implemented a comprehensive warehouse management system, including picking processes and a forklift guidance system, back in 1996. Over three decades, the system has been able to respond flexibly to the pharmaceutical company’s requirements – with one and the same warehouse management software.
As a critical infrastructure, the location is subject to particularly high security standards, including the European Union’s NIS2 directive on cybersecurity. In order to continue to meet these requirements in the future, the decision was made to replace the old system. The development of the new warehouse management system was once again to be implemented by and in collaboration with TUP.
At the beginning of 2025, the new customized warehouse management system from TUP went live on the premises of the international pharmaceutical company. The project was marked by special circumstances: After the project started in 2020, the world was turned upside down by the coronavirus pandemic. In the pharmaceutical industry in particular, in addition to many ongoing critical processes, resources had to be made available for the development and distribution of COVID-19 vaccine variants. The intralogistics IT project was put on hold and the collaboration was redirected. After the pandemic, the new WMS came back into focus. New insights gained by the warehouse staff were used to further refine the specifications and incorporate them into the processes. The result is a tailor-made warehouse management system that optimally covers process variance, transparency, traceability, and service levels.
Enormous process diversity
“Individuality is lived here – this is clearly evident in the multitude of processes,”
says TUP project manager Nicolas Walther, referring to the special features of the project. The need for highly varied processes arises from the inventory stored. Inventory management at the Karlsruhe warehouse is characterized by a demanding combination of strict specifications—particularly in regard to traceability—and many special product characteristics, including temperature sensitivity, hazard potential, and high inventory value.
Even storage in the distribution center near Karlsruhe requires the perfectly coordinated interaction of numerous interlinked processes. The most striking aspect is the topology of the warehouse: It is divided into two temperature zones – normal temperature (also known as “ambient” or ‘warm’) and “cold,” where temperatures must be kept between two and eight degrees Celsius. This spatial separation of the areas is only the first step in ensuring the ideal handling and storage temperature for each type of goods. The transport management system implemented via the TUP.MFC material flow solution controls all areas of intralogistics based on these characteristics. For example, “warm” goods can occasionally be routed through the cold area, but cold goods are never exposed to the warm area. The appropriate temperatures are also taken into account when allocating storage locations – because the higher up in the high-bay racking, the warmer it is. Temperature loggers continuously monitor the conditions. The WMS maps the high-bay warehouse into different (temperature) layers and takes this dimension into account when allocating storage locations.
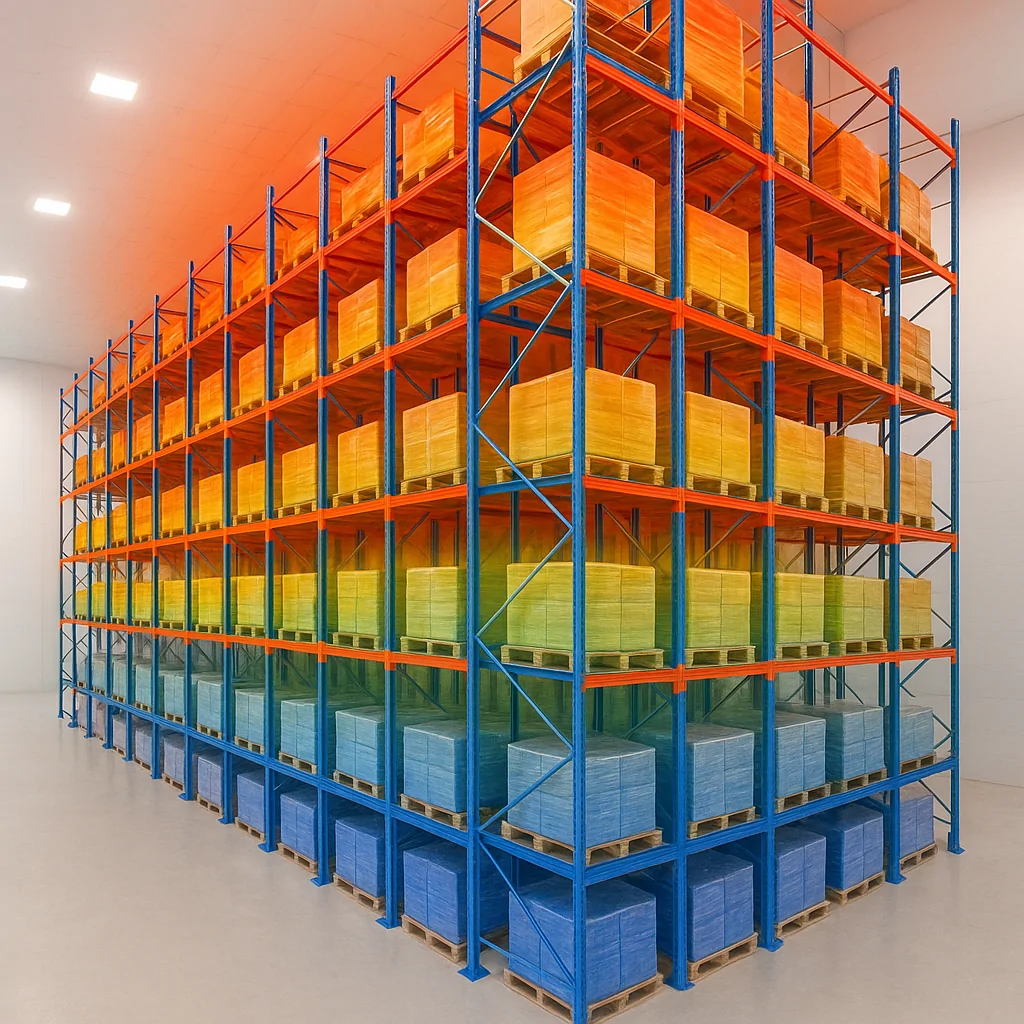
Other factors that significantly influence storage strategies:
- Classification as hazardous goods: These goods must be stored near fire extinguishing equipment.
- High-security products: These goods are stored according to separately defined specifications and are therefore protected from direct manual intervention, for example.
Physical factors: These include varying pallet heights, which influence both the number of storage locations available and the warehouse strategy.
The warehouse management system developed by TUP takes into account all the individual requirements of the product range and thus determines the ideal storage options and locations.
Delivery processes as the key
Intralogistics is of central importance for the high level of service that the pharmaceutical group offers its diverse customer base, which includes wholesalers, pharmacies, hospitals, and related stakeholders (including the veterinary sector). There are a large number of different processes, particularly in order picking: from MDE devices and automated materials handling technology to forklifts and various other technologies such as pick-by-light, different variants of goods-to-person or so-called smart picking. The latter is the counterpart to goods-to-person and optimizes the corresponding picking routes in the warehouse.
Separate storage areas, including separate picking types, enable expected peaks in demand to be processed quickly. Separate processes are also available for handling the high-security products mentioned above. All variants have been specifically implemented for warm and cold storage areas. Value-added services include the creation of customer-specific pallets and repackaging in break-proof cartons suitable for shipping.
In addition, further services are provided as part of operational processing, such as the dispatch of vaccination card information together with vaccine doses or the economically motivated cold shipping of warm-stored products. When handling products that require serialization, the serial numbers are handled according to operational requirements – either through complete recording and write-off or by providing product-accompanying data without write-off.

Service means speed, reliability, and completeness
In pharmaceutical logistics, the challenge is not to achieve the highest possible throughput, but to handle sensitive medicines correctly and ensure their timely availability. In addition to absolute process reliability, same-day shipping and delivery reliability are therefore of central importance in warehouse management. At the Karlsruhe site, cut-off times regulate this bindingly: Orders received before these times are picked and shipped in full on the same day.
The new intralogistics system ensures detailed documentation and security mechanisms that extend beyond the warehouse. The goods issue process not only includes queries that check and verify correct load securing, for example, but also records the load with which a package left the warehouse. In this way, the WMS ensures complete traceability throughout the entire warehouse.
Conclusion
Despite dynamic conditions – from constantly changing requirements to highly regulated workflows – it was possible to implement a warehouse management system that reliably masters one of the most process-intensive areas of intralogistics: Speed, reliability, and completeness are essential, while strict temperature specifications and differentiated storage and transport zones must be reliably managed.
The new WMS creates a sophisticated network of safety and plausibility mechanisms and monitors every step of the process – from temperature-controlled storage and retrieval to highly differentiated picking and supplementary value-added services. This ensures that quality and compliance remain unaffected even with high process density.
From an IT perspective, the flexibility of the solution is particularly impressive: The customized WMS offers an exceptionally wide range of system parameters that can be used to configure virtually every nuance of the operational processes. This “brutal parameterizability,” as requested by the customer, enables the system to be tailored precisely to the specific requirements of the pharmaceutical warehouse and allows a rapid response to new regulatory or business conditions if necessary. It thus forms not only the backbone of the current warehouse processes, but also a solid basis for the continuous optimization and future security of the site.
Do you have any questions?
Do you have a project inquiry or would you like individual advice?