Shopping over the Internet is part of the everyday life of most people today, and digital shopping tours using a smartphone or notebook have long since become the norm. But in order to meet the increasing number of orders placed via online shopping, mail order companies need increasingly sophisticated logistics concepts that enable them to manage their flow of goods even more efficiently. Zalando, Europe’s leading online platform for fashion, relies on the material flow control system from TUP at its Lahr location – after the recent project handover, it’s time for a summary.
In order to offer its over 23 million active customers (as of Dec 2017) the best possible service at all times, Zalando operates four state-of-the-art logistics centers in Germany alone. The newest location in the trilaterally located Lahr, in the border triangle between France and Switzerland, is impressive not only because of its size. From the logistics center in Lahr, consisting of four halls with a total area of 130,000 square meters, Zalando customers in Germany, Switzerland and France in particular benefit from even faster delivery. The material flow control system from TUP (TUP) ensures a smooth workflow. In the four logistics buildings of the distribution center, it controls the material flow between various logistics systems such as container conveyor technology, vertical conveyors, shuttle storage and outgoing goods sorters.
Order picking on five floors
The high demands of the project are particularly evident in two of the facilities in Lahr, which are intended exclusively for order picking. Here, the articles are stored on five levels, where currently around 1,000 employees, guided by their mobile data collection devices (MDT), manually pick the items. The other two buildings are processing areas. One of them houses a bag sorter with around 700,000 bags, which is used for even faster and automated picking of particularly popular articles. The other building is equipped with several kilometers of trough conveyor technology and a shuttle warehouse. Here, 22 shuttles distributed over two aisles and eleven levels with around 2,100 storage locations ensure that the articles on offer are put together without error into batches ready for dispatch. The trays remain in the warehouse or rather in the buffer only until a batch is completely assembled. The levels in each aisle are connected by a lift, which can accommodate two trays at a time. If a suitable packing station is available in goods issue, the picked trays are automatically transported there from the shuttle warehouse. The storage and retrieval of the trays is optimized and controlled by the material flow computer (TUP.MFC) from TUP.
In addition to the entire material flow control, batch management and shuttle warehouse control, TUP is also responsible for the routing of trays and parcels, parcel and item sorter control, lift control, empties management, control of the continuous scales for trays and the volume recording devices for parcels as well as the control of the labeling machines. “The batch management system mentioned above performs a special function in the TUP.MFC: The chaotically stored and picked items are grouped together in batches, and since the picking of a batch does not take place simultaneously, the TUP.MFC must collect and buffer the trays of a batch in all picking areas and, exactly when the packer needs them and then deliver them to the respective packing stations as a continuous train of trays,” explains Stefan Fehrenbach, Project Manager at TUP. Within the Zalando world, all processes are precisely coordinated in terms of time. With several million articles, stored in two picking warehouses and distributed over five levels, this is a particular challenge.
The TUP.MFC provides the employees with exactly those articles that are needed at any given time. Fast processing of orders is important because every day several hundred thousand customer orders reach Zalando’s own warehouse management system ZALOS. In practice, ZALOS is responsible for inventory management and order administration and gives the TUP.MFC orders for transports and batch destinations, and also supplies labeling as well as sorting data. Thus, TUP.MFC not only controls the material flows in the warehouse; it also simultaneously controls the supply of all demand points with empty trays, the correct feeding of trays stored in the shuttle to the packing stations, the labeling of shipping packages and the goods issue sorter.
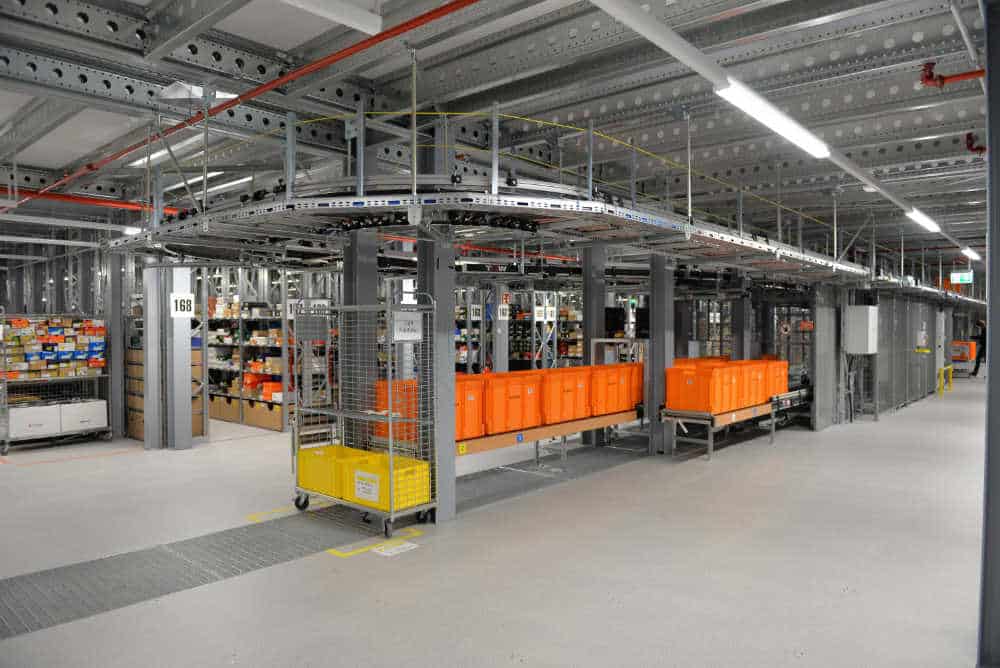
Tray conveyor technology – more than 2,000 trays per hour
The TUP.MFC controls the entire tray conveyor system. The 4,500 trays in the system enable goods receipt and dispatch to be optimized. The associated conveyor lines currently achieve an output of more than 2,000 trays per hour. In order to handle these throughputs, Zalando needs high-performance components at some neuralgic points, such as special lifters in the picking warehouse. The lifting elements, which are equipped with two load handling devices and two pick-up points each, can transport up to four trays simultaneously and distribute them between the five levels in the picking warehouse. Partial pick-ups and deliveries are possible in any combination. The TUP.MFC controls the optimal picking and delivery of the trays and checks before each picking operation whether the required delivery space is available and, if necessary, gives preference to another order. Thus the lifters are always used to full capacity.
Networking of materials handling technology, IT and software as the key to success
All systems used in the logistics center, such as ZALOS, TUP.MFC and also programmable logic controllers (PLC) are closely linked. If, for example, a tray in the goods receipt is filled, ZALOS sends a transport order to the TUP.MFC, which in turn sends a corresponding departure command to the PLC. The latter then transports the tray to the next routing point. Only then can the employee continue working. The efficient use of the hardware used thus enables a high input and output rate.
A lucrative business model: Zalando or Mode unlimited
As mentioned at the beginning, TUP had to take into account the hardware of various materials handling equipment suppliers for the control software. The logistics center in Lahr was equipped with materials handling technology from TGW, Fives and Caljan. This not only resulted in new processes for TUP in relation to the previously implemented warehouses but also in considerably more interfaces that had to be considered during the planning. “The Zalando distribution center in Lahr was and is a special project for both parties. Especially the closely timed commissioning, the tests and the successful ramp-up were equally know-how-driven, due to the interlocking with the other Zalando locations. TUP was thus able to contribute its expertise from the first Zalando logistics center in Brieselang,” says project manager Stefan Fehrenbach. “Our experience shows on the one hand that the e-commerce sector is characterized by strong seasonal peaks, a high number of returns and a diverse range of goods, but on the other hand that it cannot function without reliable software and the corresponding know-how – Zalando and TUP complement each other perfectly in this respect”.
In addition to the four logistics centers in Germany, Zalando also operates other distribution centers throughout Europe. TUP was also commissioned to implement the material flow computer for the Zalando logistics site near Szczecin in Poland. Together with TUP, the company thus ensures that customers always receive the goods they have ordered promptly – regardless of when they were ordered. Because weekends and holidays are no obstacles in the e-commerce business. In the Internet, shops are always open.