The Austrian company GRASS has built a high-tech warehouse at the new Vorarlberg location Hohenems. TUP (TUP) supported the internationally leading manufacturer of movement systems for furniture in the planning and implementation of the globally operating distribution center. The project also includes the use of TUP’s new hybrid picking system.
It is the largest logistics construction project ever realized in the Austrian state of Vorarlberg. With an investment volume of 70 million Euros GRASS GmbH has created the conditions for a profitable and sustainable development. On a 52,000 square meter site near Hohenems a distribution center has been built that uses state-of-the-art automation solutions. High bay and manual storage offer about 38,800 pallet spaces on 22 levels. Eleven aisles are laid out so that production could be added later.
With more than 200 distribution partners in 60 countries GRASS needs a solid logistical foundation. The company of the Würth Group is one of the global figureheads for furniture movement systems. But – as the company summarized – not all growth opportunities have been fully exploited due to infrastructural limitations. The objective of the largest investment in the company’s history was therefore clearly formulated: The new central distribution center was to significantly shorten reaction times; the inventories, including individualization, packaging, and customer and order-specific order picking, were to be concentrated at a high-performance location. The company was looking for a solution that would handle the entire logistics of all European production plants.
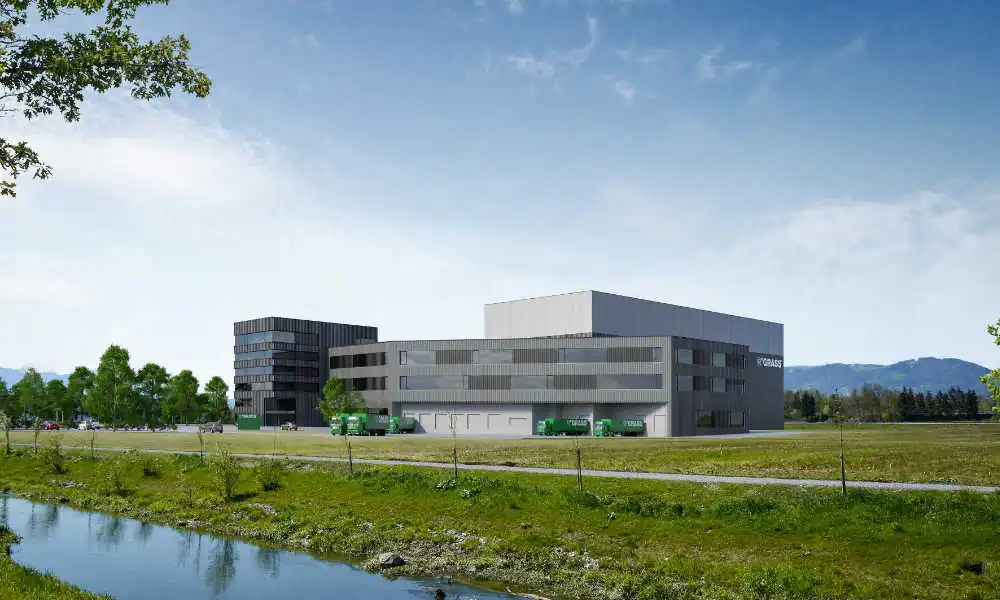
With the support of TUP’s intralogistics expertise, a modern logistics center was built from 2018 onwards to meet this requirement. Despite the corona pandemic conditions the software manufactory could prove its strength in process consulting and led GRASS on the way to an efficient intralogistics infrastructure.After having completed the requirements document together in workshops, TUP customized a GRASS-own Warehouse Management System (WMS) following the modular principle that is characteristic for the manufactory: GRALIS is based on TUP.WMS and has material flow control (TUP.MFC), mobile device connection (TUP.SML) as well as forklift guiding system.
GRALIS operates independently in the area of goods receipt: Trucks dock and the fully automated system takes in pallets without the involvement of personnel. The counterpart at the end of storage is a sequential goods issue. Using two separate double-deep dispatch buffers, tours are pre-sequenced: The retrieval is done within in a heavy before light order to optimize the loading of the truck.
Future-oriented GRASS now benefits from a multi-client and multi-location capable global system. Thus, further distribution centers can be connected without problems. Overview dialogs allow the monitoring of the warehouse operation. The dialog system can be called up web-based, therefore the user does not need a Java environment anymore and can start applications on any browser-enabled device.
The parameterization of the system was outsourced from the source code into a set of rules. This allows to define and configure rule catalogs for topics such as zone coordination, consolidation target or language of the shipping label based on specially selected criteria. The result is a very clean and easily comprehensible system. Transparency is further enhanced by storage and transport orders, as they are called at TUP. Each object transported in the facility manages its own orders: From labelling to checking to compartment search. The set of rules including this type of order is also connected to the pallet conveyor system via an interface, which ensures that actions are processed in an orderly manner. In this way, parts lists, for example, can be served ideally for the picking process.
A special feature in the common intralogistics world of GRASS and TUP is the order picking. According to the requirements of the worldwide operating Austrian producer, the software manufactory has developed a novel practice concept. “The Pick-by-Light idea was extended and implemented with a combination of overview screens and mobile devices (MDEs) instead of conventional hardware. The result is the hybrid picking system. It supports the user on various levels, including ergonomic pallet provision,” explains Eduard Wagner, CIO of the software manufactory TUP.
In this hybrid working environment, each pallet picking station is equipped with a guidance screen and permanently assigned mobile MDEs. The devices are linked together per workstation and across the entire work area and communicate as a unit with the conveyor system. The screens guide the user visually and at the same time provide him with a multimedia overview; in real-time he receives further information on the current pick and his work list. Via detailed MDE dialogs he can also interact directly with the WMS GRALIS. “Additional tasks, such as customer-specific requests, can be made immediately accessible and implemented during the picking process,” Wagner adds. Through the TUP solution GRASS benefits from the advantages of the different picking approaches.
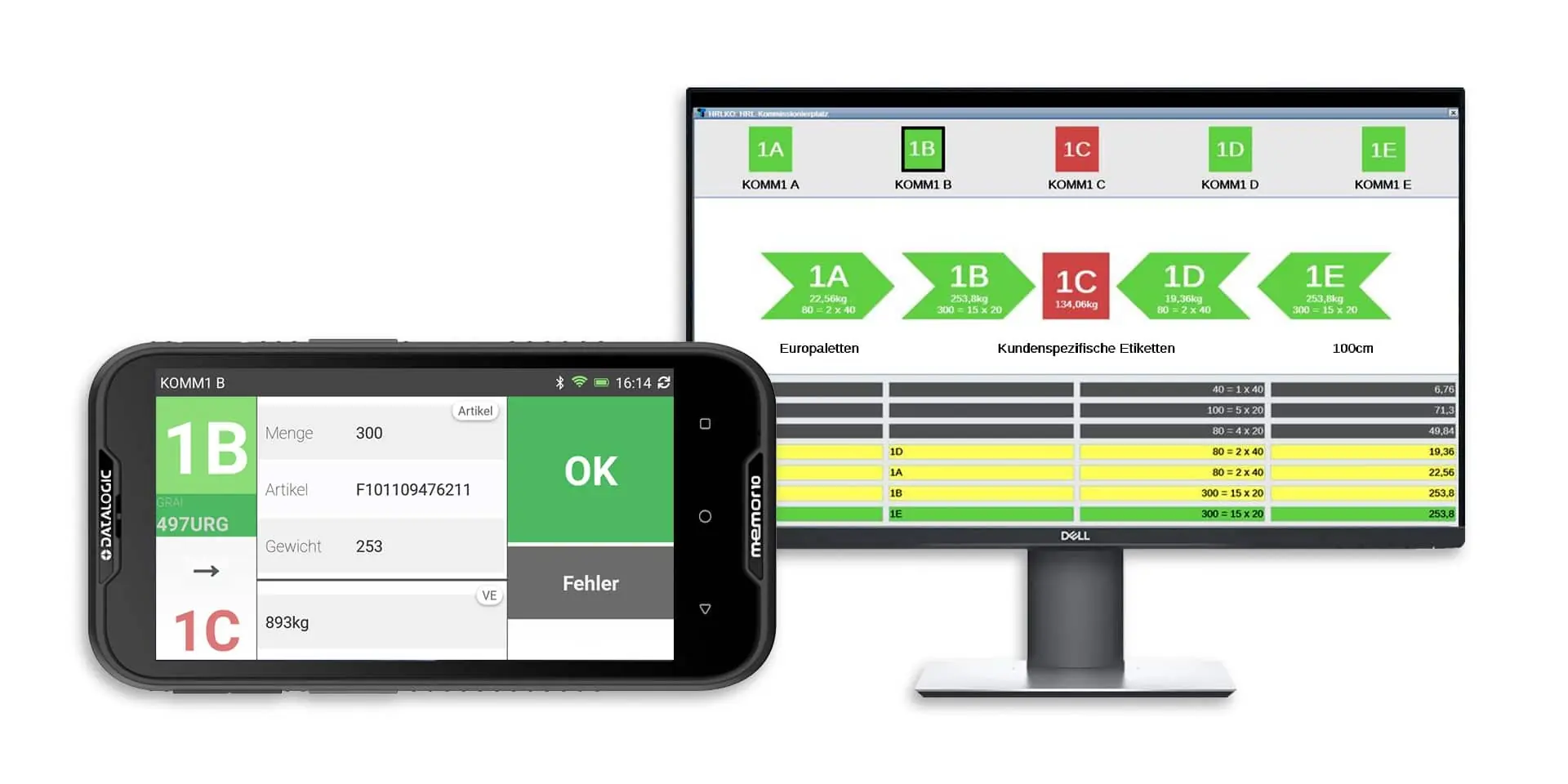
“Optimizing the supply chain management is a key challenge in order to be sustainably successful”, the GRASS management had announced in the context of the announcement of the new building. With the new structure of GRASS’ intralogistics, supported by TUP, nothing stands in the way of this aspiration. At the end of the joint project stands a modern distribution center which truly meets the requirements of a globally operating company.
This project report also appeared in the 11/12 issue of the intralogistics trade magazine ‘materialfluss’. You can find the PDF of the published german-speaking article here.