In der Interview-Reihe sprechen wir mit Mitarbeitern der GRASS-Gruppe über die Zusammenarbeit im Projekt Zentrallager Hohenems. Im zweiten Teil der vierteiligen Reihe steht das Gespräch mit Jürgen Moritsch, dem Experten für die strategische Logistik der GRASS-Gruppe im Mittelpunkt.
Was ist deine Position und deine Aufgabe bei GRASS?
Ich bin seit 2007 bei GRASS in der Logistik tätig und bin aktuell für die strategische Logistik in der GRASS-Gruppe verantwortlich.
Wie kam es zur Initiierung des Projekts?
Ich wurde beauftragt als Projektleiter eine Ausschreibung für das GRASS-Zentrallager in Hohenems zu initiieren. Dazu haben wir zwei Ausschreibungen vorbereitet, einmal für die Logistik und einmal für die Software. Um die richtige Idee zu finden, haben wir einen Ideenwettbewerb initiiert und mehrere Anbieter angeschrieben. Gemeinsam mit ihnen haben wir viele Konzepte erarbeitet und überwacht, um uns dann am Schluss für ein Projekt zu entscheiden.
Dieses Projekt war dann das Zentrallager?
Wir haben aus diesen vielen Ideen dann für uns die beste ausgesucht, indem wir alles aus den vorhandenen Erfahrungswerten und was uns in der Implementierung besonders wichtig war ins Projekt mitaufnahmen. Das Ergebnis ist die Variante, wie wir sie jetzt im Einsatz haben. Das war auch die richtige Entscheidung.
Was wäre ein Beispiel dieser Besonderheiten, die auf jeden Fall berücksichtigt werden sollen?
Für uns war wichtig, dass wir die Transporte unter den Werken mehr automatisieren. In der gesamten Anlage war uns wichtig, dass wir von vielen manuellen Tätigkeiten in die Automatisierung kommen. Es sollte beleglos sein. Die Mitarbeiter sollten in der Kommissionierung und im Picking durch die Software unterstützt werden, vor allem darin welche Tätigkeiten als nächstes ausgeführt werden. Auch die ganzen internen Prozesse sollten verknüpft sein, damit wir das operative Personal überall einsetzen können. Das war uns sehr wichtig.
Wie lief die Planung aus deiner Perspektive ab und zu welchem Zeitpunkt stieß TUP dazu?
Wir haben die Software, wie bereits erwähnt, ausgeschrieben. Dort gab sehr viele Anbieter, am Ende haben wir über ein Auswahlverfahren den jetzigen Anbieter TUP ausgewählt, um mit ihnen ins Rennen zu gehen. Wir hatten durch die vielen Gespräche ein sehr gutes Gefühl, dass die Software-Manufaktur für die Zukunft der richtigen Partner ist.
Gab es da Argumente oder Situationen, die für dich den Ausschlag gegeben haben?
Es war nicht meine Entscheidung, es war eine des Teams. Aber wir haben in diesen Gesprächen sehr gut vermittelt bekommen, dass das was wir ausgeschrieben haben, von der Angebotsseite auch so schlüssig war, dass es reibungslos umgesetzt werden kann. Auch die Referenzen waren so, dass es gepasst hat.
Wie war die Zusammenarbeit mit TUP?
Ich hatte eigentlich immer ein gutes Gefühl in der Zusammenarbeit. Wir haben uns gegenseitig ausgetauscht, wenn wir auf unterschiedliche Sichtweisen gestoßen sind. Die erarbeiteten Lösungsansätze waren immer die, bei denen wir sehr sicher sein konnten, dass sie der richtige Weg waren. Die operative Zusammenarbeit mit den Kollegen vor Ort war für uns immer sehr angenehm. Da hat es nie große Reibereien gegeben.
Gab es da eine besondere Situation, bei der man sich über eine Diskussion einer guten Lösung angenähert hat?
Wir verwenden Trays auf den Paletten. Da war der Ansatz im Projekt, dass wir jede Palette mit einem Tray ausstatten müssen und jede Palette auf diese Trägerpalette verheiraten müssen. Das war für mich nicht tragbar. Da waren die Diskussionen mit Herrn Pirulli sehr interessant, aber er konnte sich dann überzeugen lassen, dass die Variante nicht so umsetzbar ist, weil er es selbst testen konnte. Danach haben wir das Problem gemeinsam gelöst.
Wie hast du den Hochlauf empfunden?
Wir waren in einer schwierigen Situation durch Corona. Bestimmte Testphasen liefen nur über Webex und Video-Telefonie. Hier hat man gesehen, dass die Zusammenarbeit gut funktioniert hat. Wir konnten alles umsetzen und alles war erklärbar. Der Hochlauf an sich war sehr gut. Wir haben in Phasen durchgetestet: Zuerst den Wareneingang, dann die nächsten Prozesse durchgeführt und getestet. Neue Themen kamen erst dran, wenn wir gesehen haben, dass alles Bisherige funktioniert. Es war uns sehr wichtig, dass der Hochlauf und die Zusammenarbeit mit Umsetzern und Hardwarelieferanten so reibungslos wie möglich funktioniert. Was dann auch die Situation zur Inbetriebnahme war.
Wie war die Situation mit der Anlage der Leerpaletten im System?
Wir musste eine Lösung finden, wie wir die Ware auf der Palette verheiraten. Der Tray hatte den Grundbarcode, über den wir ihn mit dem Lademittel verheiratet haben. Alles was mit diesem Tray passiert, konnte so über die gesamte Wegstrecke verfolgt werden. Die Herausforderung war, dass diesem System dann Leerpaletten zugeführt werden müssen. Das erfolgte über Zehner-Stapel. Es war so angedacht, dass wir für jede Palette, die auf eine Trägerpalette verheiratet werden muss, einen Leerstapel bilden, weil wir das später in der Kommissionierung benötigt hätten. Das war aber nicht umsetzbar, nach drei Mal scannen war die vierte Palette falsch. Wir mussten also eine Lösung finden, über die wir dem System mitteilen „Ich bilde jetzt einen Zehner-Stapler, aber ich habe nur die Trägerpalette als Kennung für das System“. Das war für TUP in der Umsetzung dann nicht direkt klar, wir konnten es aber schnell lösen, weil wir es vor Ort durchtesten konnten. Im Endeffekt wurde die Lösung, dass nur die Trägerpalette gescannt wird und dementsprechend die Information hinterlegt wird, ob es jetzt ein Leergutstapel ist oder nicht.
Was war deine Erwartungshaltung gegenüber TUP zu Beginn des Projekts und während der Umsetzung?
Wir hatten die Ausschreibung sehr umfangreich gestaltet und haben daraufhin ein sehr gutes Angebot von TUP erhalten. Dementsprechend war unsere Erwartungshaltung, dass TUP weiß, was sie tun. Software ist für einen Logistiker oft ein Niemandsland, da braucht es Experten. Daher haben wir viel Wert darauf gelegt, dass wir die richtige Unterstützung von Seiten der Software-Anbieter erhalten.
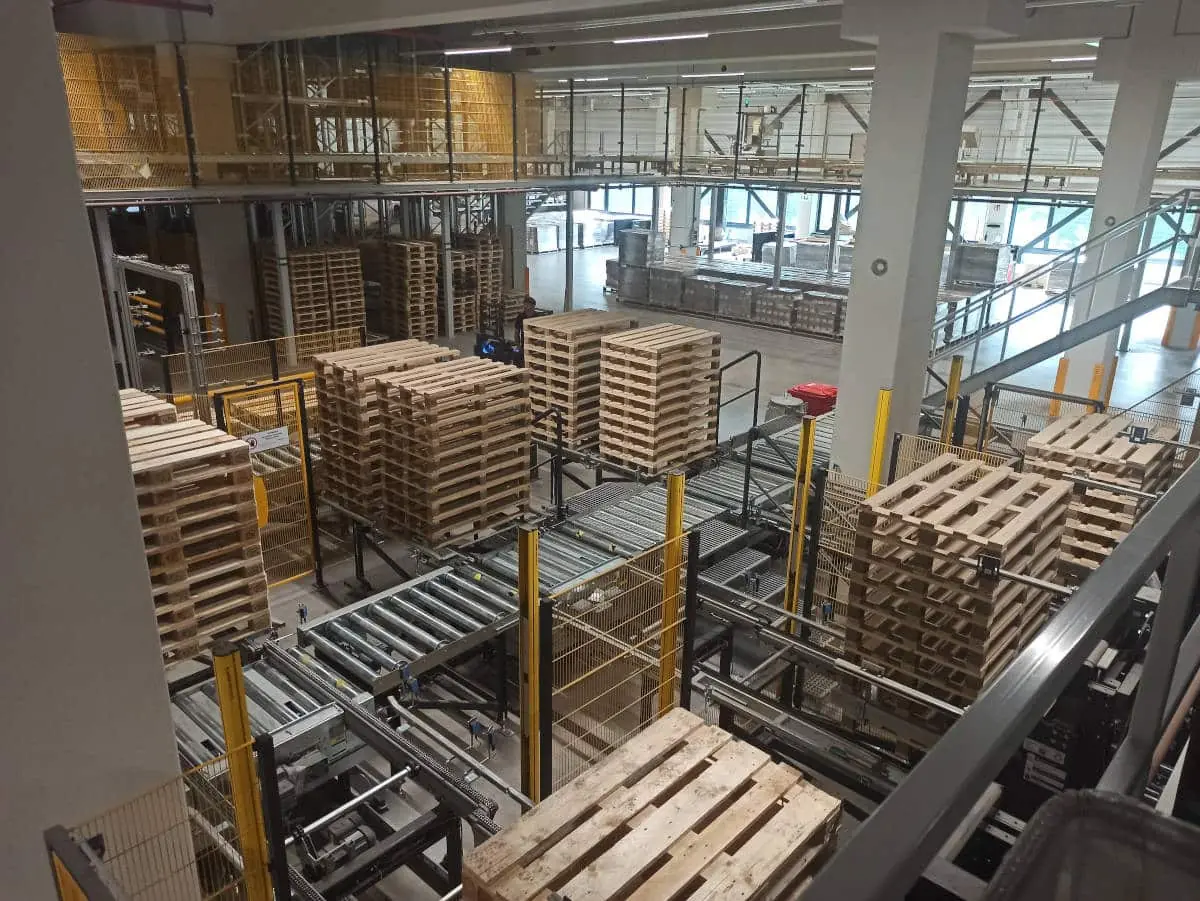
War ein Teil der Erwartungshaltung, dass das Vorgehen genau erklärt wurde?
Ja, was das anbelangt, will ich wissen, wie das System funktioniert. Ich muss es nicht auf der technischen Seite vollständig durchdringen, aber ich muss wissen, was geschieht und warum es geschieht. Das wurde auch immer wieder erklärt und wir haben immer die richtige Antwort auf unsere Fragen erhalten. Wenn etwas erklärt wurde und wir haben etwas nicht verstanden, konnten wir problemlos nachfragen und bekamen dann auch die Information. Das war auch wichtig, weil wir so die Prozesse beruhigt weiter ausbauen konnten. Wir haben auf alles eine professionelle Antwort erhalten und wurden nie mit der Aussage „Wir machen das für euch und ihr nehmt das“ abgespeist.
Wie wurde auf geänderte Anforderungen durch die Projektbeteiligten reagiert?
Wir haben geänderte Anforderungen offen diskutiert. Wenn es machbar war, haben wir es ins Projekt integriert. Wenn es nicht mehr machbar war, wenn der Eingriff zu tief gegangen wäre und den Projektfortschritt gefährdet hätte, dann haben wir es hintenangestellt. Was nicht bedeutet, dass wir es außer Acht gelassen haben. Alles wurde in Jira-Fällen dokumentiert, um nach der Inbetriebnahme die Anforderungen nochmal zu bewerten und bei Bedarf zu integrieren. Das war auch gut so, denn so wurde die Inbetriebnahme nie gefährdet und wir konnten trotzdem einige Verbesserungen noch während des Projekts integrieren. Wir hatten nie das Gefühl, das Dinge vom Tisch gewischt wurden. Die Vereinbarungen, das bestimmte Dinge später gelöst wurden, waren immer einvernehmlich.
Wohin geht der weitere Weg für das Projekt?
Wir haben während der Hochlaufphase schon sehr viele Verbesserungen durchgeführt. Wir wollen uns zukünftig in der GRASS-Gruppe mit der Software von TUP pro Werk ausbreiten. Im Augenblick prüfen wir die Hardware und dann werden wir mit den Anforderungen aus der Produktion nochmals ein Software-Projekt starten, um das umzusetzen.
Gibt es da besondere strategische Fokuspunkte, die sich abzeichnen? Mehr Automatisierung oder selbstfahrende Systeme?
Hier im Zentrallager haben wir viele vorbereitende Schritte getroffen, um die Erweiterung der Werke anzugehen, wie beispielsweise ein Staplerleitsystem. Hier wurde alles durchgetestet, was wir in den Werken auch umsetzen können. Ziel ist mehr zu automatisieren und beleglos zu arbeiten. Dazu brauchen wir die entsprechenden Voraussetzungen, um das umzusetzen. Das Ziel ist, dass vom Zentrallager die Kommunikation in die Werke einfließt, die bestimmt, wie die Ware zu uns kommt. Also nicht mehr der Kundenauftrag in den Werken aufschlägt und dann produziert wird.
Wohin geht der weitere Weg für dich?
Für mich war es so, dass ich das Zentrallagerprojekt umsetzen durfte. Ich war derjenige, der die grüne Wiese erarbeitet hat und es zur Umsetzung gebracht hat. Es war immer klar, dass ich nach diesem Projekt wieder in meine Funktion der strategischen Logistik zurückgehen werde. In Zukunft werde ich mich wieder auf die Werke konzentrieren, um da die angesprochenen Automatisierungen und Verbesserungen in den Werken umzusetzen. Dazu bin ich jetzt als Fachexperte für Logistik freigestellt worden, um die Werke dorthin zu bringen.
Das klingt nach einer spannenden Herausforderung!
In jedem Fall! Von Stammdaten bis hin zum Gebinde-Management gibt es da viel zu tun.
Vielen Dank für das Interview
Hier geht es zu den weiteren Interviews.