The range of coverage is a key figure that expresses the internal security of supply through a company’s own stocks of a particular item within a specific period of time. The range of coverage indicates how long a stock level is still sufficient to fulfill existing orders. This in turn indicates when the corresponding inventory or materials need to be reordered. While the significance, relevance, and consequences are different for manufacturing companies than for trading companies, the common goal remains to avoid both too short and too long a range of coverage.
Calculating the range of coverage
Data from internal systems within a warehouse management system is used for the calculation. To do this, a specific period of time in the past is analyzed to determine the average stock and the average demand per time unit.
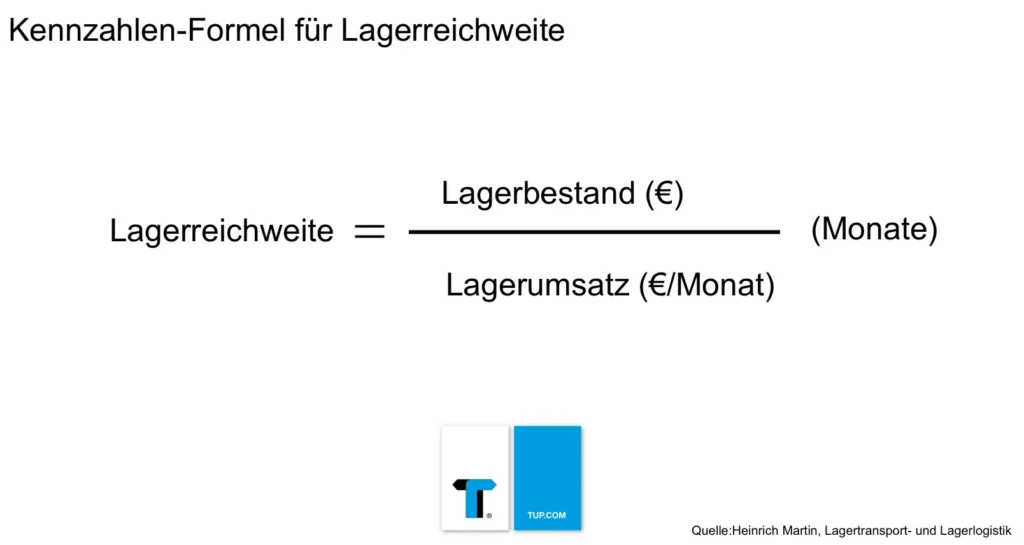
The range of coverage is calculated using different formulas.
If three red T-shirts in size M are ordered per day and 21 of these identical items are in stock, then the range for this article is seven days. This means that delivery bottlenecks of new T-shirts in size M can be compensated for seven days and that the orders for one week can probably be fulfilled.
Two alternative calculation formulas include further specific planning data, but focus on different reference values:
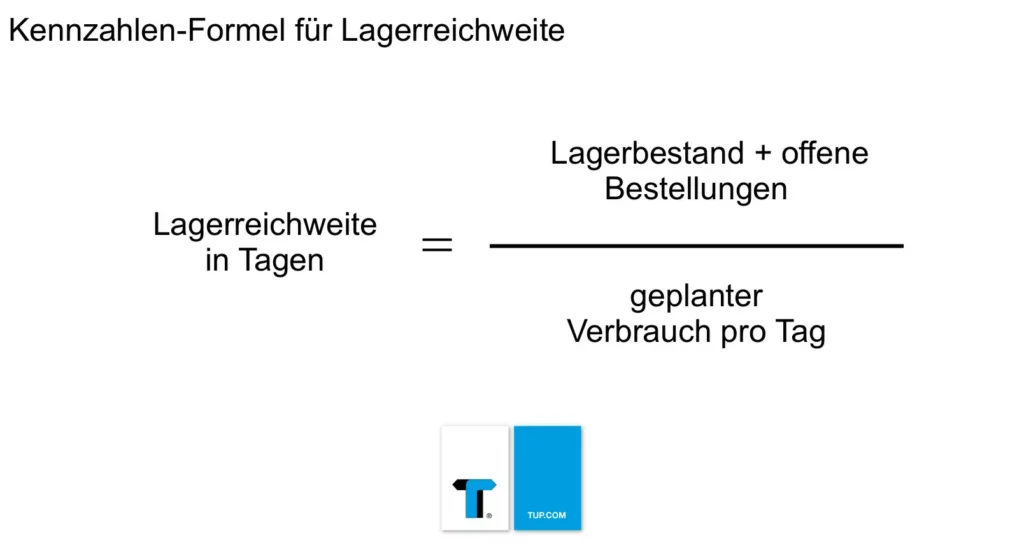
The range of coverage in days can be calculated using open orders.
If an average of three red T-shirts are ordered per day and there are 21 T-shirts in stock, this formula also includes an express order for seven T-shirts. This results in a range of coverage of 2.8 days. The range of coverage is therefore more than halved by a single order.
In the third formula, the ‘action radius’ refers to the reciprocal value of the turnover rate. Heinrich Martin, Transport and Storage Logistics, 8th edition
