Industrie 4.0 – Verheddern wir uns im eigenen Datennetz?
Mathias Thomas im Pressegespräch auf dem Materialfluss Kongress 2014
Ich bin ehrlich gesagt etwas verwundert, dass wir das Thema „Industrie 4.0“ im Bereich der Logistik gerade wie eine neue Offenbarung zelebrieren. Das liegt vermutlich auch daran, dass neue Wortschöpfungen, speziell in Verbindung mit angeschlossenen Release-Nummern, in mir ein befremdliches Gefühl auslösen. Denn meistens werden nur dann neue Begriffe erfunden, wenn die Erfinder nicht genau wissen was sie da eigentlich tun oder tun wollen.
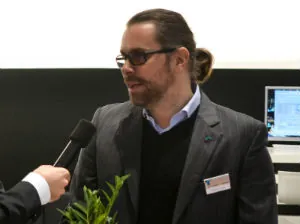
Der Fokus der aktuellen Industrie 4.0-Bemühungen liegt ja auf der Produktions-Automatisierung. Man spricht von der vierten industriellen Revolution, die uns nach der Automatisierung, der gezielten Prozessteuerung hin zur Massenfertigung (wie beispielsweise dem Taylorismus) und der Digitalisierung Anfang des 21. Jahrhunderts, jetzt in völlig neue vernetzte Sphären katapultiert. Aber das Industrie-4.0-Phänomen zieht ja viel größere Kreise. Jede Branche spricht von 4.0. Was mich irritiert: Was glauben die Leute, was wir in der Logistik die letzten 15 Jahre gemacht haben?
Die Intralogistik ist schon lange vernetzt
In der Intralogistik, speziell in der Produktionslogistik, ist das Erfassen von Daten über Durchlauf, Nachschub, Zustände der Anlange, freie Kapazitäten der Fördertechnik, Status von Maschinen und letztlich die automatisierte Steuerung – sowohl der Anlage als auch der internationalen Supply-Chain – basierend auf diesen Daten, seit mehr als zehn Jahren fester Bestandteil unserer Expertise bei TUP. Der Unterschied zu früher ist, dass die Server heute noch am Internet hängen und sich der CEO den Status jeder Maschine und den Standort jedes Mitarbeiters, in Echtzeit, auf dem Golfplatz abfragen oder ändern kann.
Industrie 4.0 ja, aber weniger ist manchmal mehr?
Was man sich in dem Zusammenhang auch bewusst machen sollte: Wir machen uns damit ein Stück weit gläsern und angreifbar, denn was der Chef kann, können andere mit hoher Wahrscheinlichkeit auch. Spätestens seit Edward Snowden wissen wir, dass es 100%ige Sicherheit nur in den Broschüren der Systemanbieter gibt. Industriespionage ist, speziell im Bereich der Produktion, zu einem der mächtigsten Wirtschaftsverbrechen avanciert. In einem Beitrag im Handelsblatt Ende 2013 spricht der ehemalige Innenminister Friedrich von einem geschätzten Schaden für die deutsche Wirtschaft von 50 Milliarden Euro – jährlich! Und dennoch verglasen wir immer mehr Türen.
Das soll nicht in eine Paranoia ausarten, sicher ergibt die Vernetzung von Produktionseinheiten und der zugehörigen Supply-Chain an vielen Stellen Sinn, erhöht die Produktivität und erleichtert globale Produktions-Prozesse. Was mich stört ist, dass jetzt gerade jeder 4.0 ruft und in jedem zweiten Portfolio irgendwelche ollen Kamellen als „das nächste große Ding“ verkauft werden. Darüber hinaus halte ich es in der Intralogistik für sehr fraglich, ob wirklich jede Schraube mit dem Internet verbunden sein muss und ob über jeden Mitarbeiter ein Bewegungsprotokoll gespeichert werden sollte. Das ist sicher ein riesen Spaß für den Controller und auch die Hardware-Lieferanten freuen sich über ein paar zusätzlich verkaufte Festplatten und Sensoren. Als Planer und Realisierer stellt mich das aber vor zwei Probleme:
Erstens muss ich dem Kunden sagen, dass sein Projekt aufgrund von technisch überdimensionierten Maschinen, neuer Netzwerktechnologie, mehr Servern, erweiterter Sensorik, speziell geschultem Personal etc. deutlich teurer wird, als es eigentlich sein müsste (was speziell bei Retrofit-Projekten eine exorbitante Kostensteigerung verursacht). Und das alles, ohne ihm dabei einen wirklichen kaufmännischen Nutzen erklären zu können. Ein paar zusätzliche Grafiken rechtfertigen keine neue Großinvestition. Die KPI der Geschäftsprozesse haben wir schon lange über andere Messgrößen ermittelt, also werden eigentlich nur weitere wertvolle und endliche Rohstoffe „verbraten“.
Zweitens bedeuten viele Daten auch viel Datenaufkommen und entsprechend schlechtere Reaktionszeiten – oder eben immer größer dimensionierter Hardware. In einem modernen Distributionszentrum arbeiten wir mit Reaktionszeiten im Millisekunden-Bereich, was die Informationsverarbeitung und Entscheidungsfindung der Fördertechnik betrifft. Deshalb ist mein Ansatz eigentlich: Weg von Big Data, hin zu (relevantem) Small Data. Oberstes Gebot ist die Erarbeitung und Pflege sauberer und klar definierter Prozesse und Schnittstellen – im Bereich der Intralogistik beispielsweise vom Wareneingang bis zum Warenausgang. Wenn für jeden einzelnen Geschäftsprozess klar definiert ist, welche Eingangsdaten für diesen Prozess und welche Ausgangsdaten von diesem Prozess wirklich relevant sind, können genau diese Informationen als Arbeitsgrundlage für alle angeschlossenen Systeme dienen und um ein Vielfaches schneller verarbeitet und interpretiert werden, denn es müssen nicht erst die relevanten Informationen aus einem Big-Data-Berg extrahiert werden. Kombiniert man diese schlanken Informationen jetzt mit Gewerke-übergreifenden Standards, wie beispielsweise SAIL, der standardisierten Systemarchitektur der Intralogistik, schaffen wir agile und modulare Anlagen, die sicher und effizient Arbeiten können. So erreichen wir eine saubere Daten-Grundlage auf Prozess-Ebene, die für alle weiteren Vernetzungen verwendet werden kann. Das ist für mich dann eigentlich schon Industrie 4.1 und die anzustrebende Zukunft.
Theorie und Praxis sind zwei paar Stiefel
Ich möchte betonen, dass bei der Industrie 4.0-Initiative klar unterschieden werden muss zwischen der Forschung und dem, was heute am Markt tatsächlich umgesetzt wird. Institute, wie beispielsweise das FML hier in München, haben das Recht, oder gar die Verpflichtung, in vielen Bereichen auch mal über den Tellerrand zu schauen. Wir in der Industrie müssen dem Kunden am Ende des Tages aber wettbewerbsfähige Angebote unterbreiten und nebenbei echten Mehrwert für dessen Geschäfts-Entwicklung generieren. Aus der Vergangenheit haben wir gelernt, dass eine Adaption von der universitären Forschung in die Industrie oftmals nicht so einfach ist, wie uns das die Theorie glauben lassen möchte.
Nichtsdestotrotz sind es oftmals die Anregungen aus der Forschung, die es uns ermöglichen, Systeme zu entwickeln, die technisch solide und gleichzeitig flexibel genug für die Anforderungen der Zukunft sind.
Bildquelle Teaser: © Nmedia – Fotolia.com.jpg